Together with the Distributed Design Platform, Happylab supports creative talents working at the intersection of design and the maker movement. From September 2022 to February 2023, the Distributed Design Residency took place at Happylab, where we supported makers and designers in the realization of their projects. The final results are impressive projects that will be exhibited in our makerspace during March 2023!
Six months of Distributed Design Residency have flown by! We congratulate our 8 residents on their great projects and present them to you in detail here. If you want to marvel at the projects in person, you still have until March 31, 2023 to stop by at Happylab!
The Distributed Design Residency will go into the next round starting in September 2023! The Open Call runs until June 10, 2023 - we are looking forward to your applications!
Feel Refill (MAria Levitsky & Daniil Chechin)
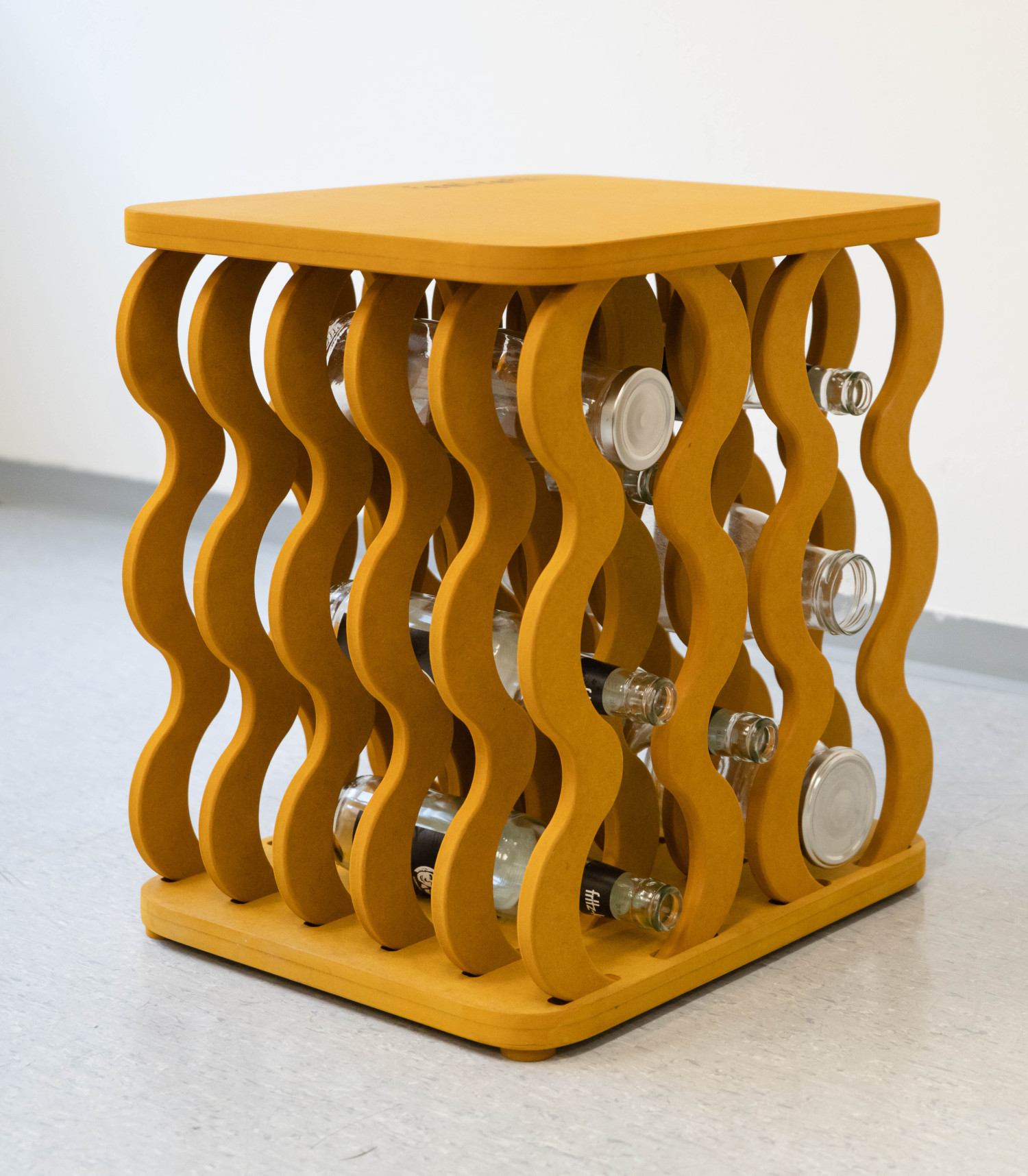
Feel Refill is a sustainable furniture project of PROSTOR Studio (Maria Levitskaya & Daniil Chechin). offers a design solution that aims to make garbage sorting more appealing and motivate people to act in everyday life.
Feel Refill was designed as a stool with the additional function of storing bottles under the sitting surface. Eight bottles of 1-litre fit in between the openings created by the wave-shaped elements. The stool is compact and can be used as a sitting place anywhere in the apartment. For instance, you could place it in the foyer as a reminder to bring deposit glass or recycled goods to the collection point. MDF (Medium-density fibreboard) was chosen as the building material because of its versatility. The material is simple to process with different digital fabrication tools or using hand and power tools. It has a homogeneous structure and therefore it is possible to use a wide range of finishing techniques.
"During the residency program, we successfully produced 3 prototypes improving each variation in terms of the efficiency of material use, minimizing finishing labour and improving the design quality. In our vision Feel Refill is a prefabricated furniture piece of different colour variations that could be easily assembled by any person without tools. But for those who are interested in building on your own, we are kindly sharing the project using open-source tools."
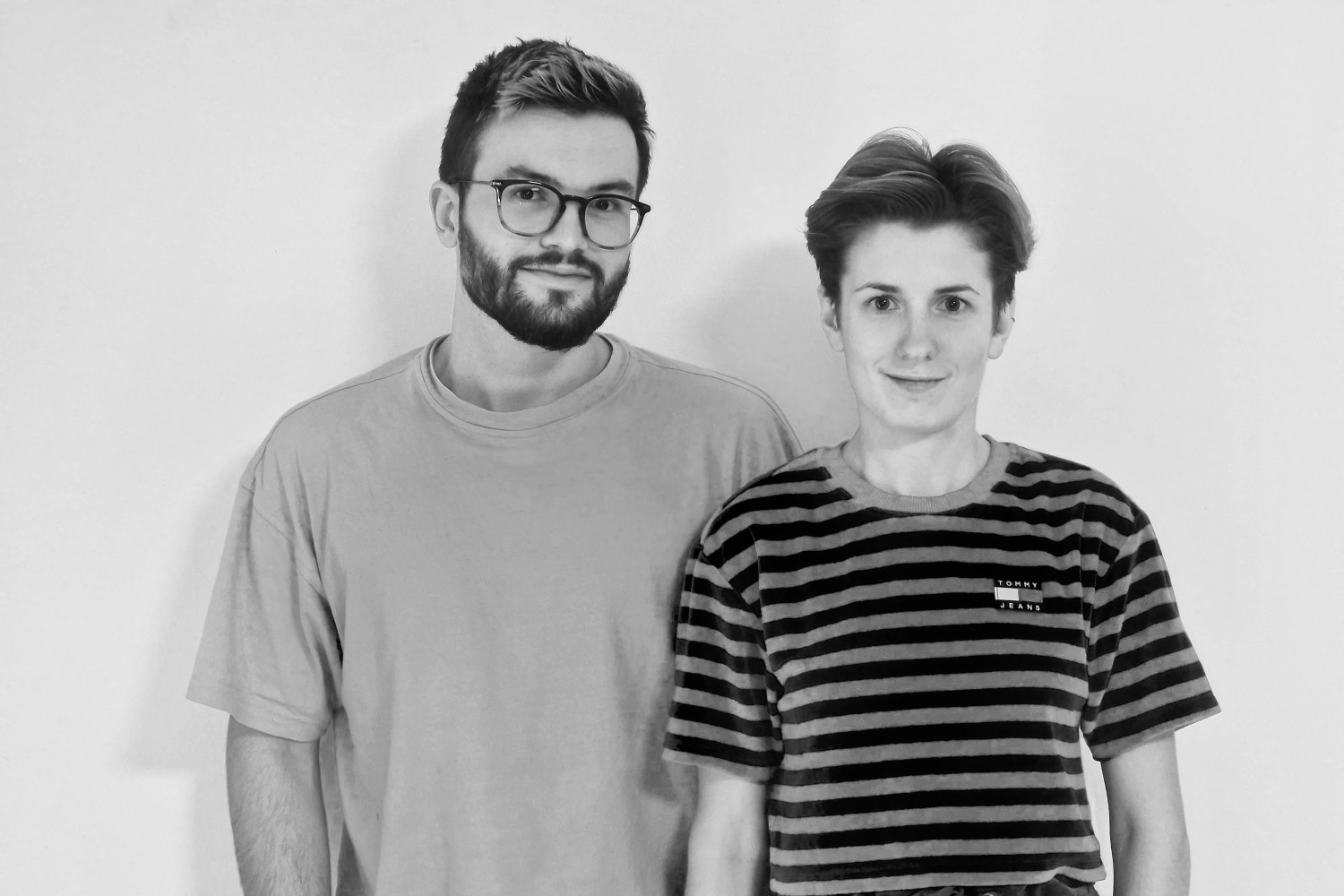
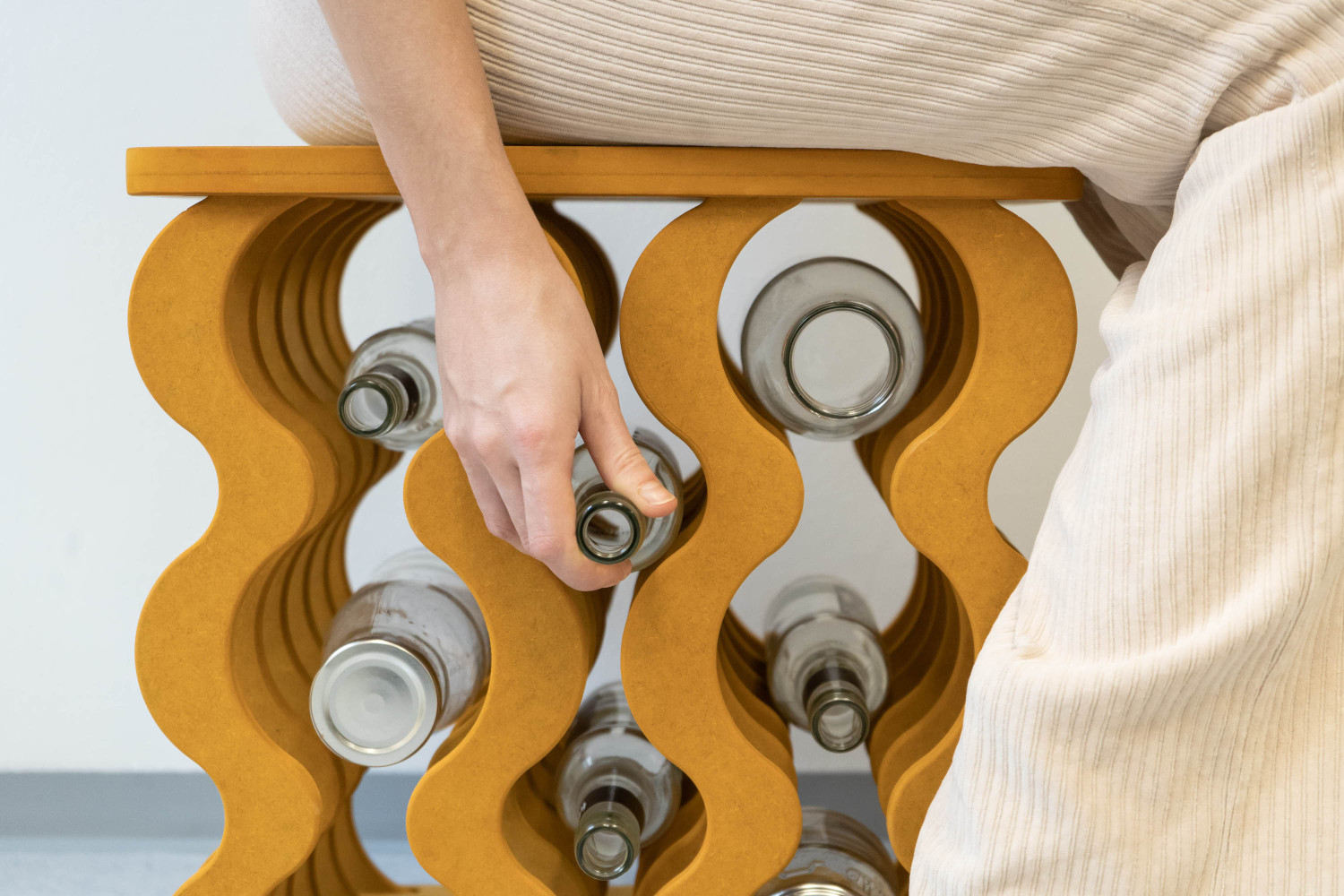
TMBR Scooter (Katrin Batko)
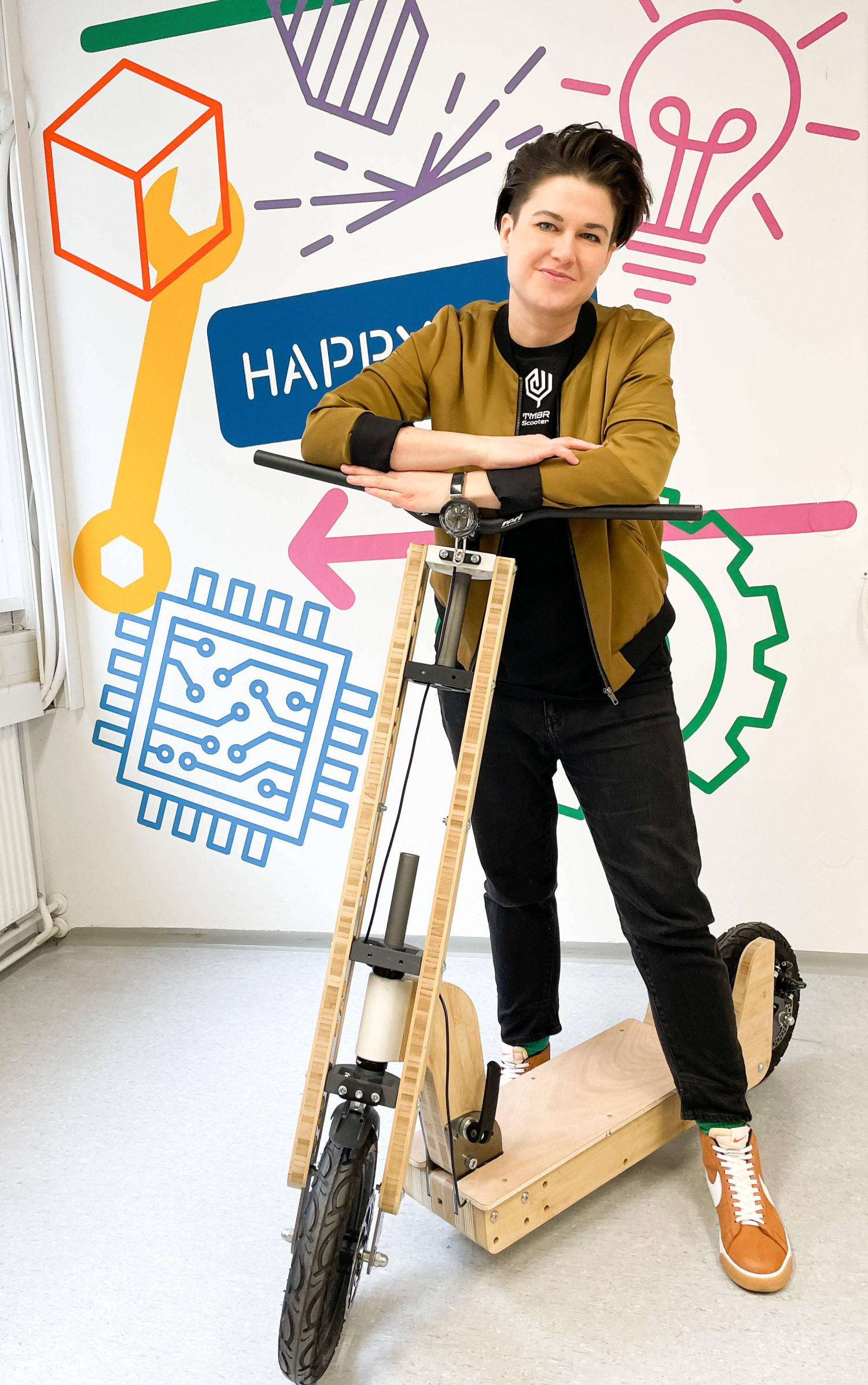
Katrin Batko is working on micromobility concepts in the city. In 2015, the idea to build a scooter came up. At that time, a first prototype was already created in collaboration with a bicycle frame builder, but unfortunately Katrin lacked the time to continue. E-scooters were also not really on the market at that time and it was very difficult to get electronic parts like motor and wheels. In 2021 the idea reignited and since then Katrin has been working on TMBR Scooter - a sustainable e-scooter with a frame made of modular elements that can be produced regionally.
Wood and bamboo from regional retailers are used for it. A key point is the design, which is fundamentally different from scooters available on the market and gives the e-scooter a new value - as these are often treated like disposable products. To take this aspect even further, Katrin uses bicycle parts available on the market, such as handlebars, stems and headsets, so that it is easy to repair or adapt the parts. Most e-scooter manufacturers almost exclusively use parts tailored to their own product, which makes swapping and repairing partially impossible. A first prototype of TMBR Scooter was created at Happylab during the last months. Laser cutter, metal laser, metal and wood workshop, CNC mill, 3D printer and the finishing area in the Makerspace were used for it.
"As part of the Distributed Design Residency, I had a lot of time to test different materials on the machines at Happylab. Especially on the metal laser I shed a lot of sweat and "tears". It is a great advantage to have the project workspace directly on site and also to be able to store the various parts and tools. By spending more time at Happylab, I got to talk with many other members and received valuable input and feedback. The collaboration and support from the Lab Managers has also been great. Before I started the residency, I was very unconfident on the Acctek CNC mill. Now I dare to mill plates with it myself without any problems."
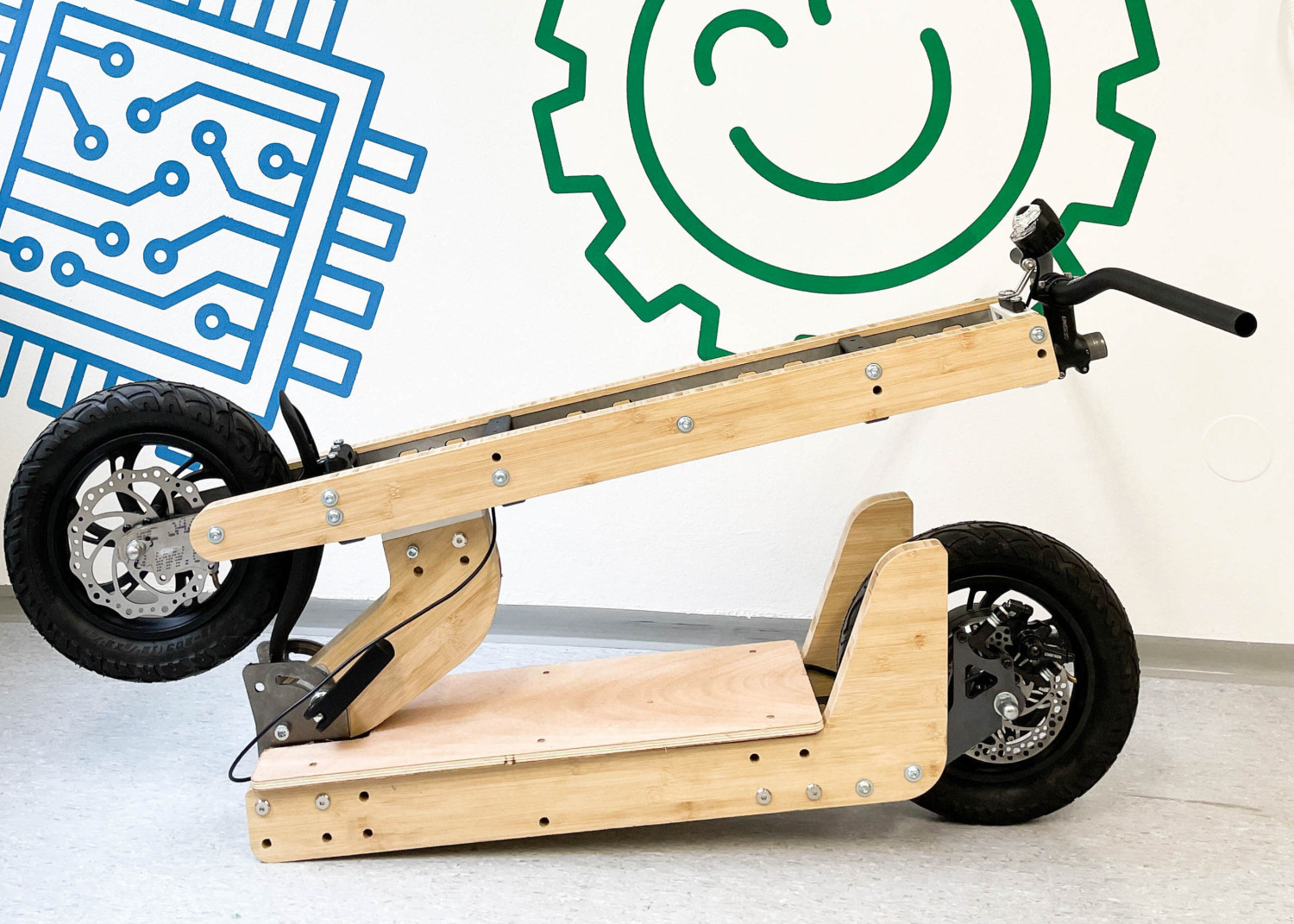
Mini Motoz - Design, Innovation und Sustainability (Robert Poeckh)
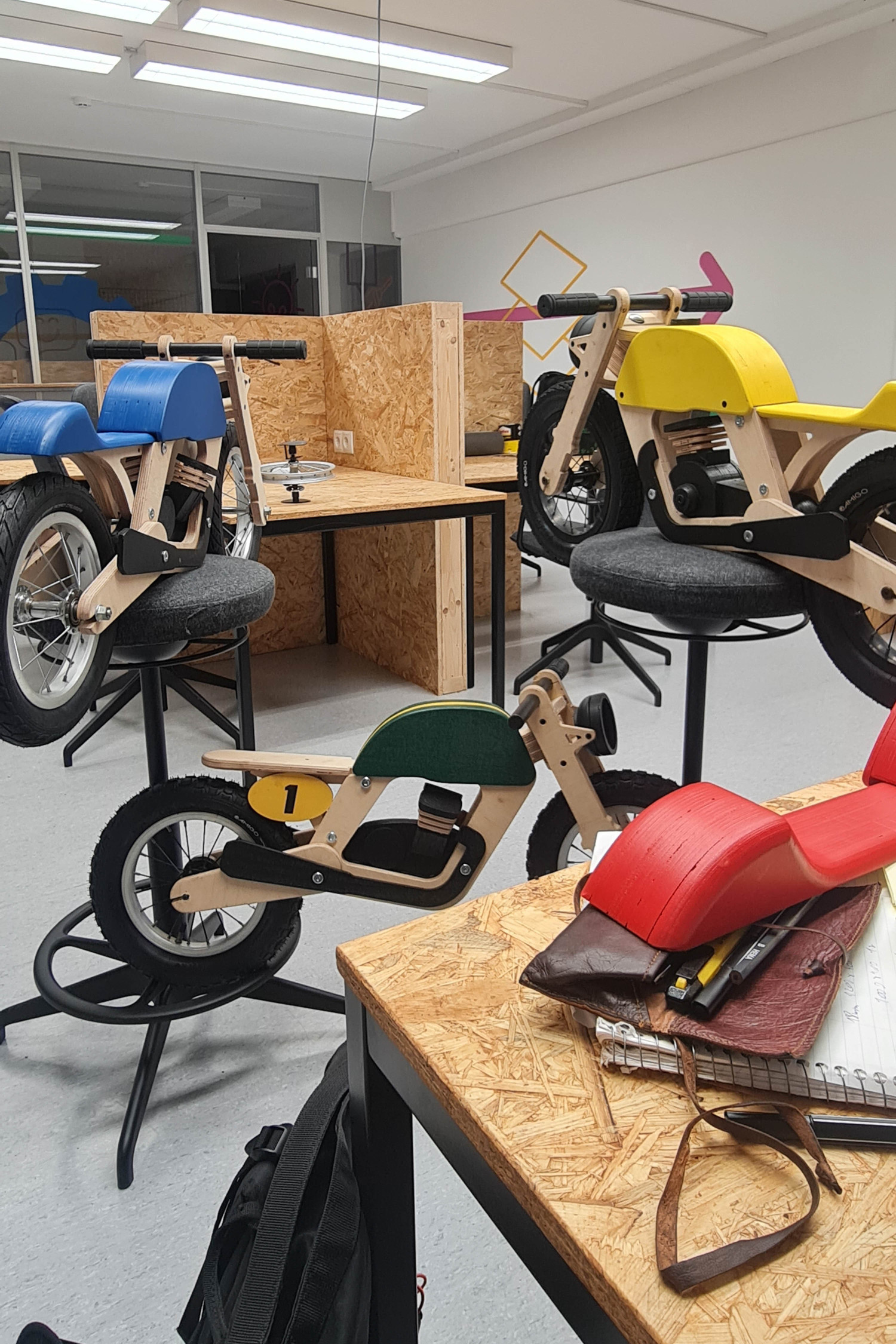
Mini Motoz are unique handmade wooden mini motorcycles that are not only sustainable but also durable. By using traditional wood craftsmanship in combination with modern manufacturing techniques such as CNC milling and laser cutting, small unique pieces are created in limited quantities. The goal was to use innovation and creativity to develop balance bikes for kids that would delight little riders and big adults alike with their quality and aesthetics.
While in the co-working space materials were ordered, parts designed and production planned, wooden parts were engraved with the Trotec lasers in the makerspace, and the patterns for the imitation leather seats were cut out. The individual leather pieces were then sewn together on the sewing machine using foam and fleece. With the help of the Prusa 3D printers, in addition to many small gimmicks around the project, e.g. a stand as well as individual jigs were printed, which greatly simplify the finishing of the wooden parts. Over 53 of the 69 individual wooden parts that make up one bike were milled from multiplex boards using the Acctek CNC mill and then reworked on the bench router, glued, sanded and painted in the finishing room. In the hobby workshop, the tube and tires were mounted on the rims and inflated. In the end, the bikes were assembled there. In addition, band saw - metal and wood - crosscut saw, plotter, embroidery machine, belt sander, stand drill were also used.
"In short, without Happylab and the combination of machines and manufacturing techniques, the project would have been almost impossible, if not impossible at all."
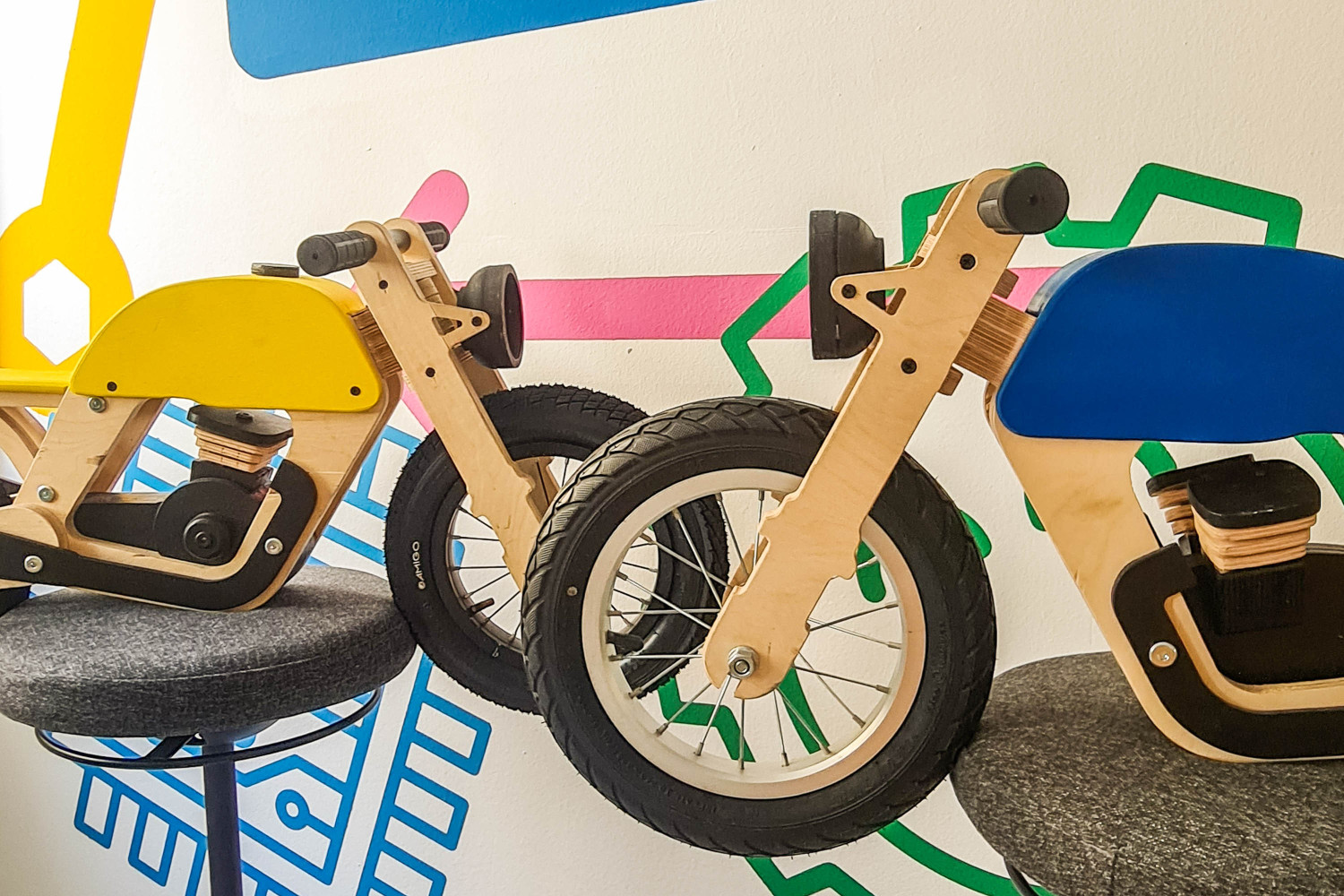
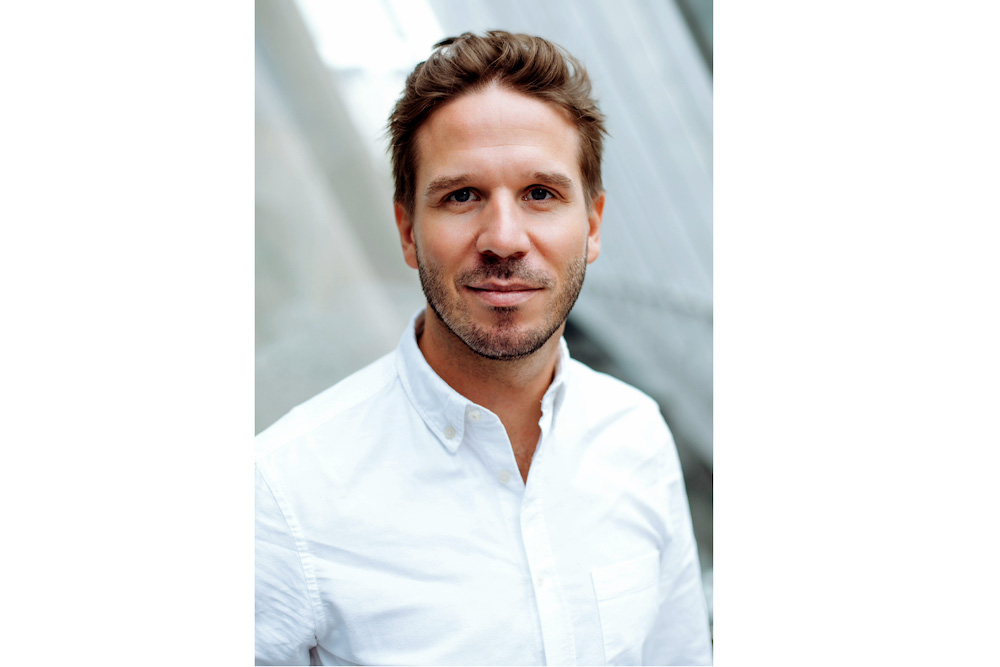
QuadO Jewellry Collection (Konstanze Prechtl)
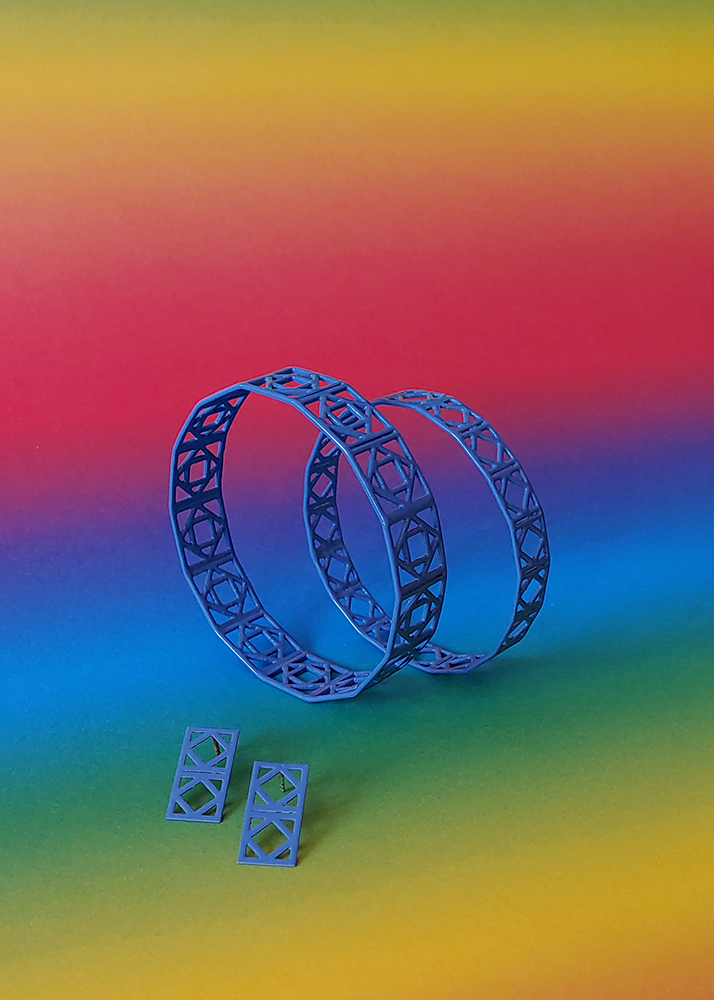
QuadO is the new jewelry collection made of stainless steel, brass & silver by freelance artist & jewelry designer Konstanze Prechtl.
Konstanze's design process usually starts with a rough sketch and a paper model. This helps her to see how the whole thing could look in three dimensions. In the next step, she uses digital drawing programs to create the final designs. The models are cut out flat on the metal laser and then shaped by buckling. The pieces are then trimmed and further processed in Konstanze's studio. Which means, they are filed and sanded, bent into shape and, if necessary, soldered or connected with ear studs. In the final step, the pieces are then powder-coated.
In the designs of the new collection, Konstanze has taken up a form that she has recently implemented in larger works (paintings, jewelry and objects): cuboids and cubes that are slightly cut and whose shape oscillates between two- and three-dimensionality.
"I've had the laser cut pieces made abroad so far, but I really wanted to do this myself - both to make everything locally as much as possible, and to experiment with different materials and sheet thicknesses. The Distributed Design Residency has helped me further develop the jewelry collection by being able to work on the machines myself."
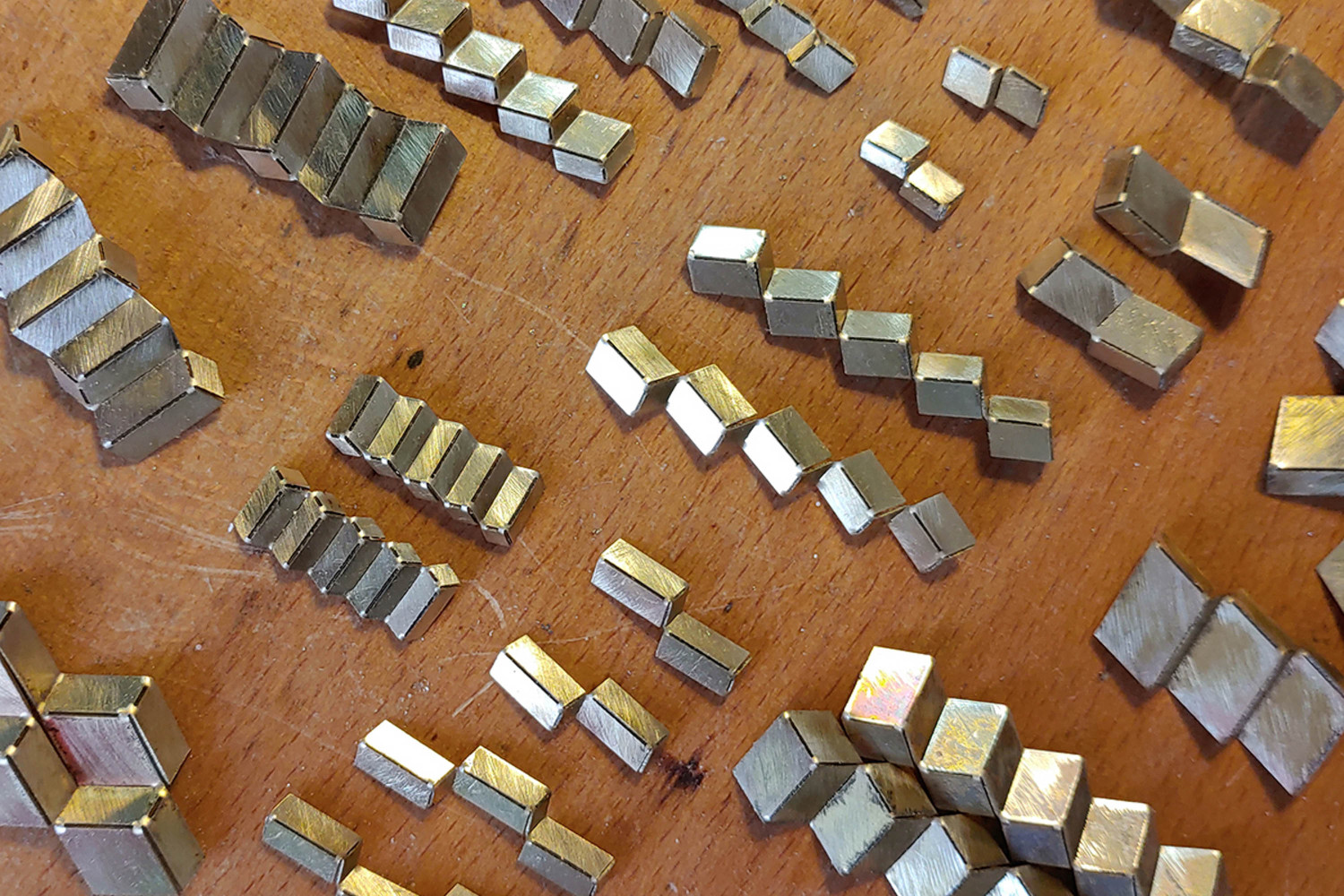
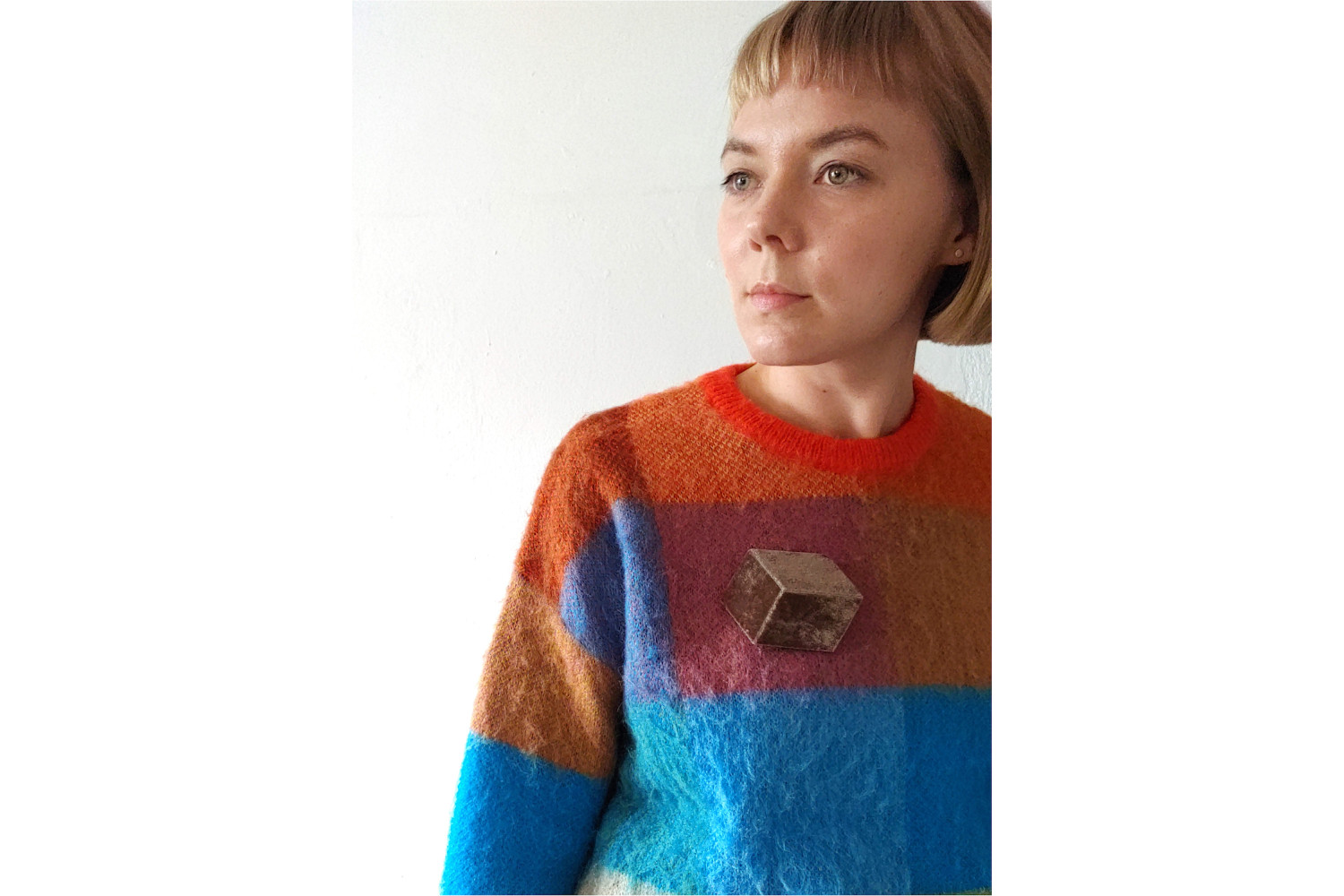
Biomaterials (Cindy Fodor)
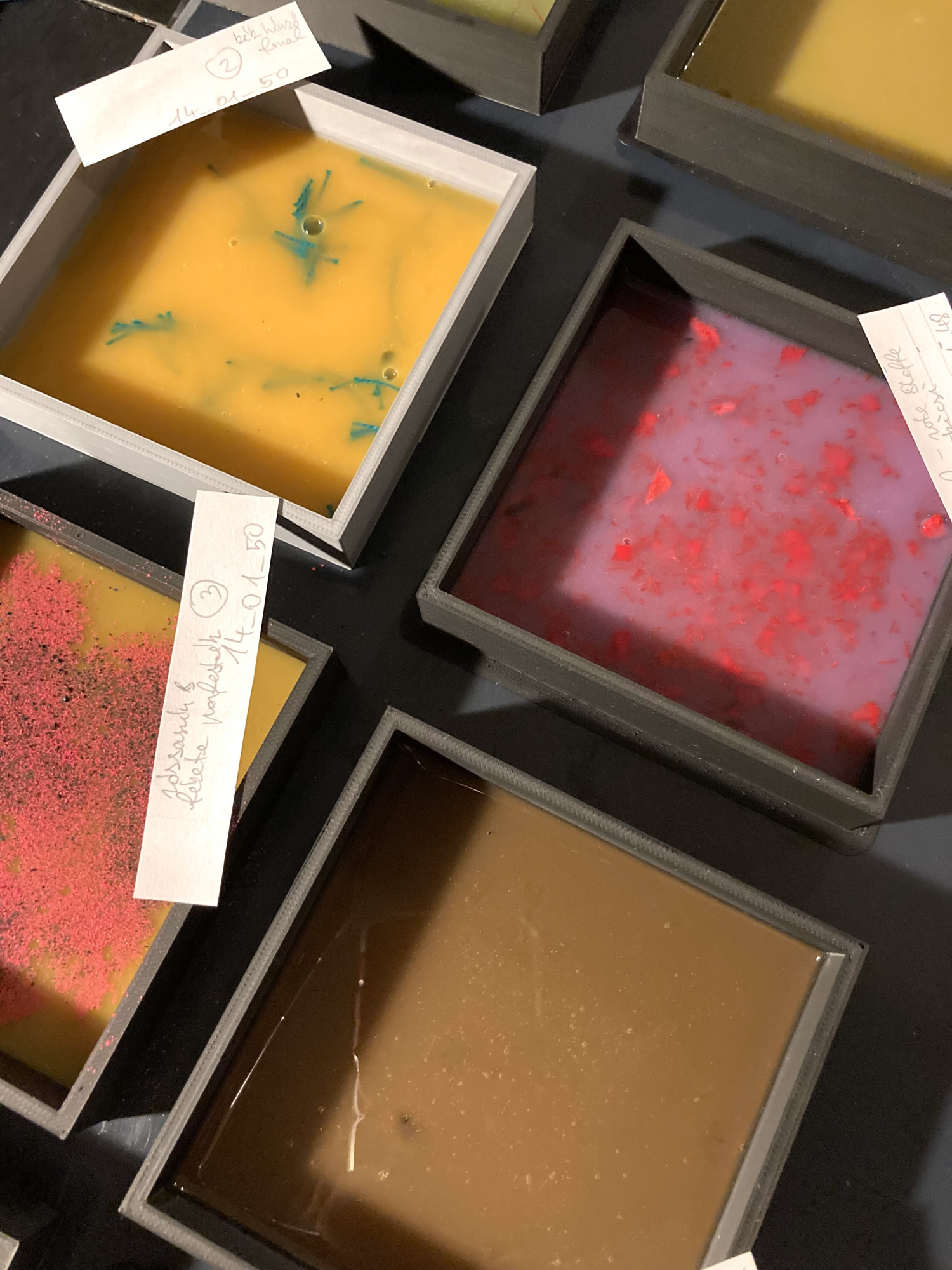
Cindy Fodor is a fashion designer. She likes to work with her own hands, but also with new technologies. At Happylab, she has already experimented with our 3D printers and laser cutters for her fashion collections. For the future, Cindy plans to experiment with biodesign and biomaterials. The Distributed Design Residency was the starting point for this!
For her experiments, Cindy has worked with many different ingredients. Three of them that were used a lot: Alginate, Agar agar, and Gelatin. The ingredients are cooked, mixed, and then the mixture is cast into molds and hardened. The custom Petri dishes were created on the 3D printers at Happylab and feature special 3D patterns to shape the surface of the biomaterials.
Cindy has documented her process and results in a "Biomaterials Cookbook," which she is happy to share with interested parties upon request!
"My goal for the Distributed Design Residency was to set up a home lab where I could experiment with biomaterials and make some samples myself. I also created a biomaterials cookbook so anyone interested in the field can get started."
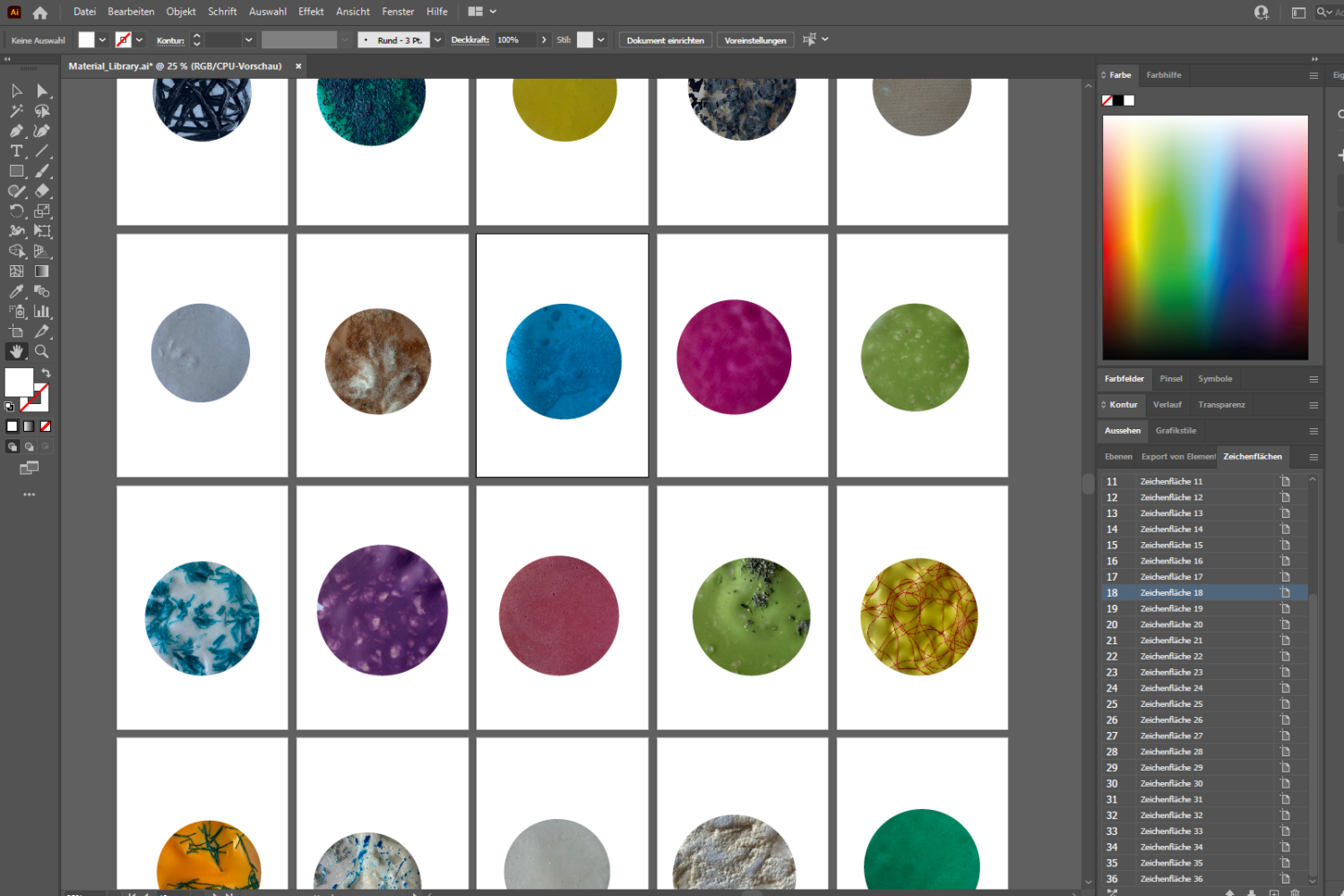

Alles Spitze (Stephanie Edelhofer)
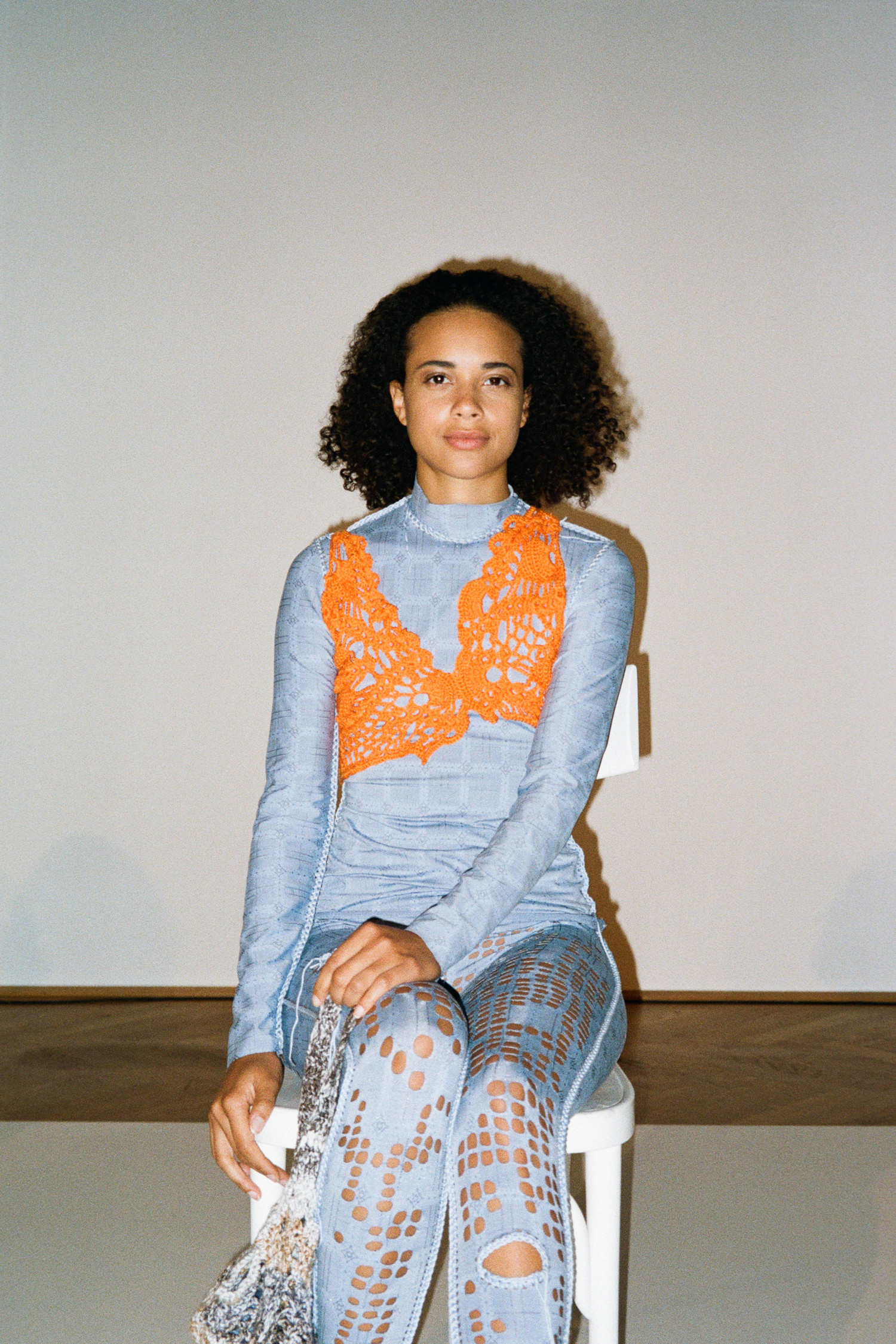
The project "Alles Spitze" by Stephanie Edelhofer addresses the socio-cultural attribution of value to textiles and presents a design for clothing production independent of corporations. The transfer of the "open source" idea is to find its way into the fashion sector by making patterns freely available for download, which can be implemented with the help of laser cutting, without much textile know-how. Following the aesthetics of lace, which used to be reserved for the wealthy social classes, digital manufacturing now makes this material accessible to all. "Alles Spitze" advocates local production and social collaboration.
For the implementation of the project, Stephanie was mainly busy at the laser cutter and also used the sewing machine at Happylab little bit. She was excited by the idea of "mimicking" the aesthetics of lace using laser technology. Stephanie has also used the Distributed Design Residency to explore other areas and gain new knowledge. In the future, the open source patterns will be available for download on her website.
"The daily conversations with other residents were very fruitful and it was nice to see the process moving forward with everyone. The Happylab staff has always been there to answer questions and offer support in a great way. Thanks here especially to Lukas who seems to be so patient all the time."
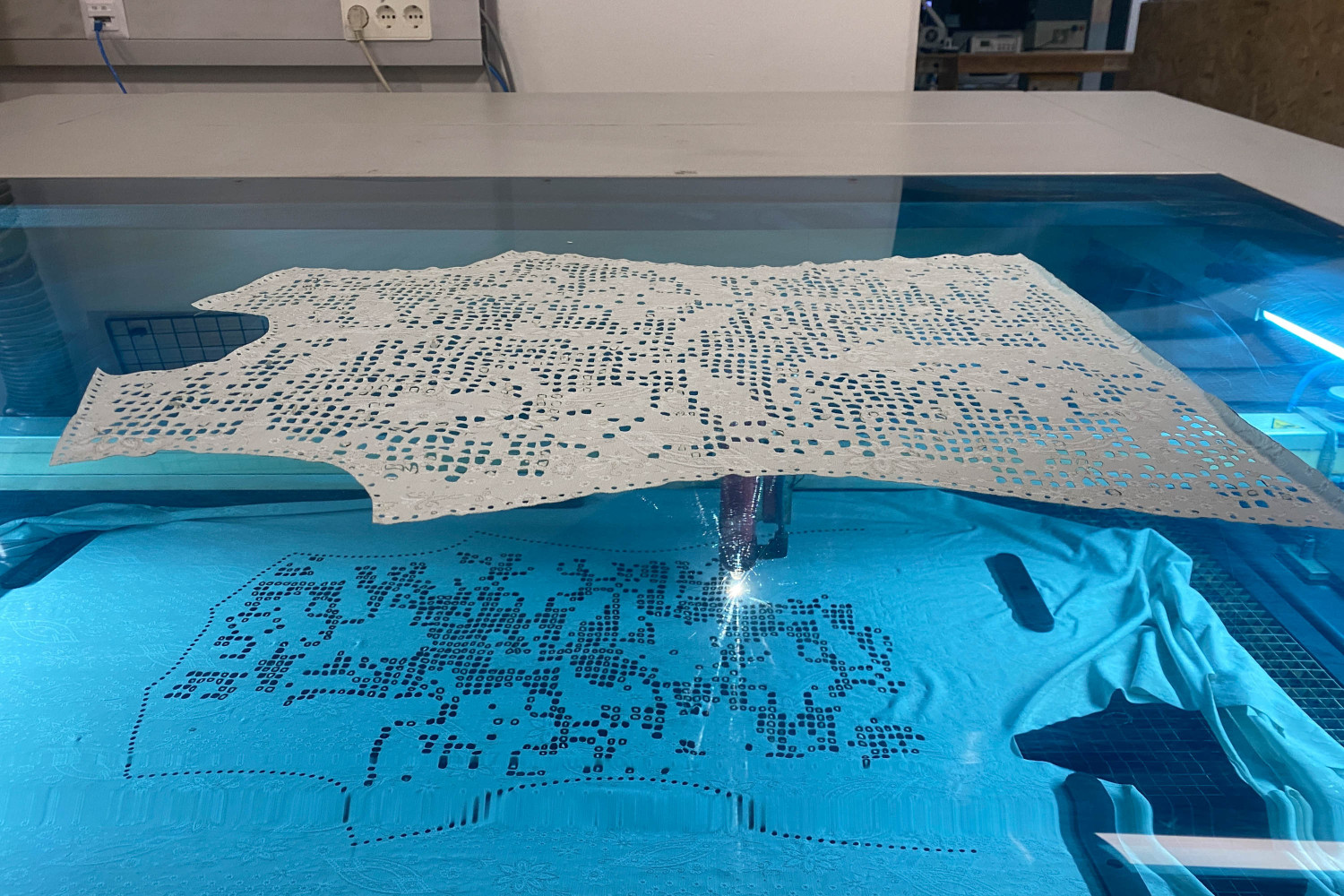
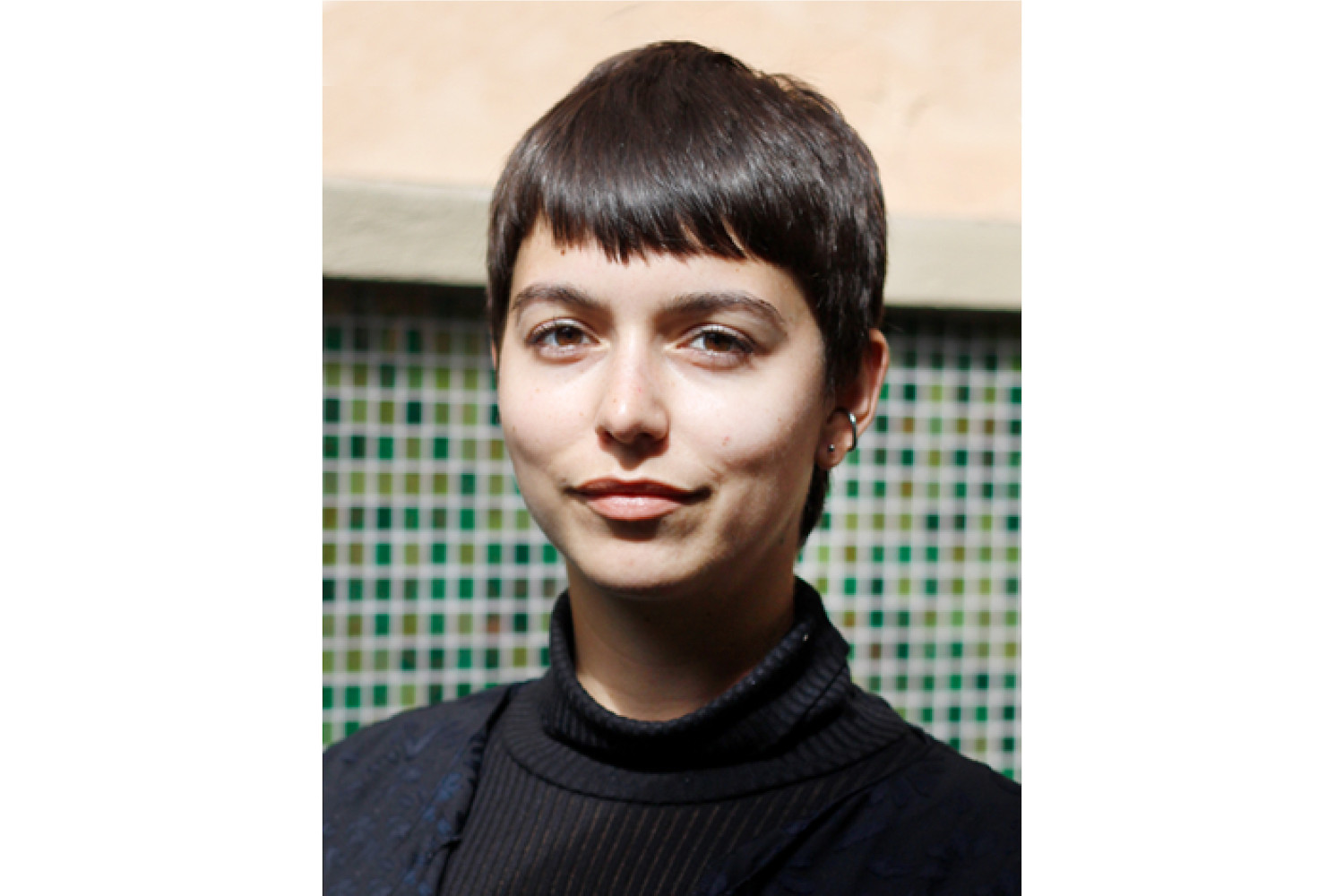
Pregnancy Massage Table (Katharina Gleißberg)
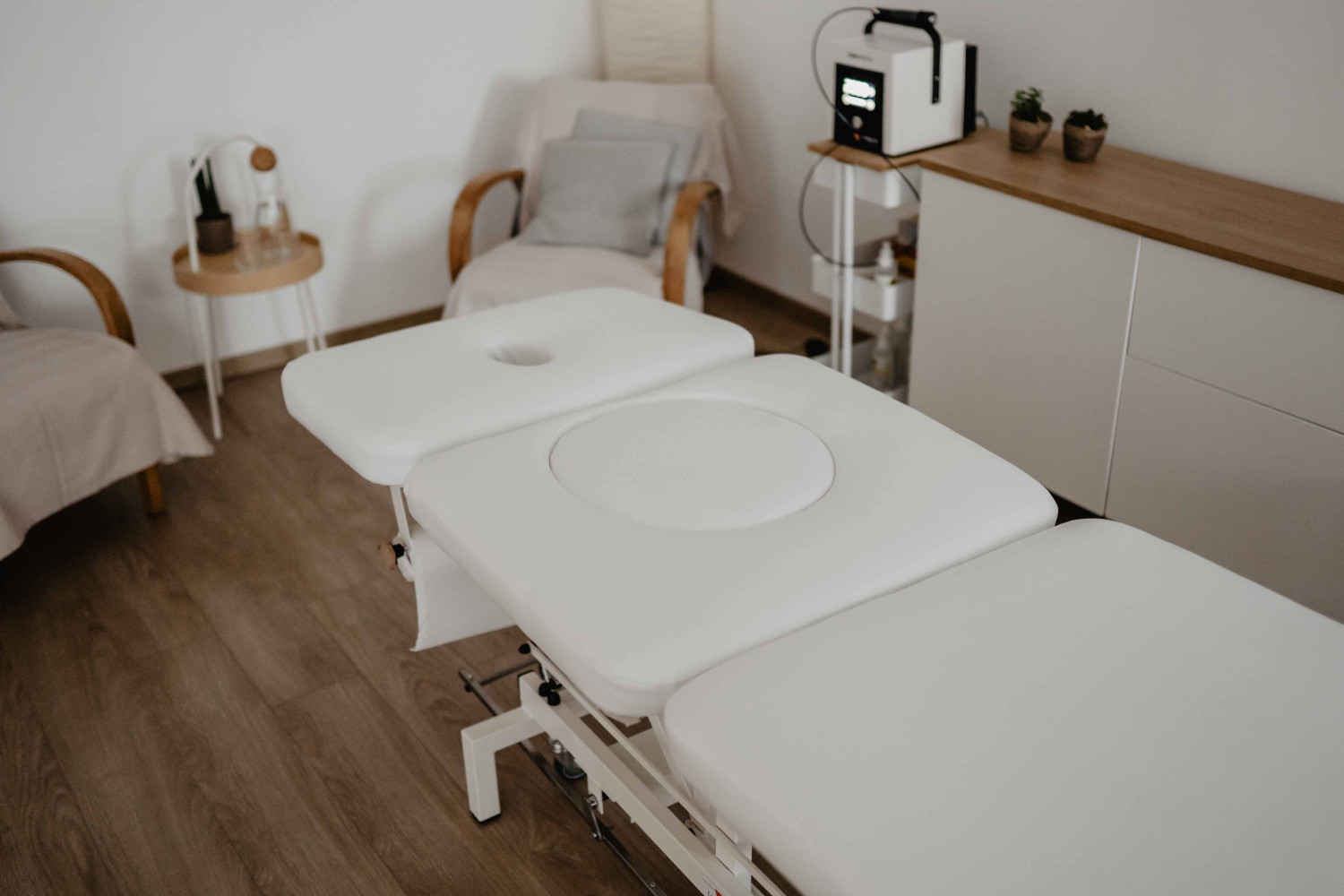
After years of working in the field of therapist massages and many pregnant patients, Katharina Gleißberg thought about designing a cushion for electric massage tables, which can simply be screwed onto the base of the existing table. The highlight - the hole for the pregnant belly. The belly is held in place by an adjustable cloth to fit any cavity.
At Happylab, Katharina used the CNC milly, laser cutter to cut the foam parts and sewing & embroidery machine to create the leather cover.
"Especially the co-working space and consulting hours as part of the Distributed Design Residency were great, likewise networking with each other was awesome!"
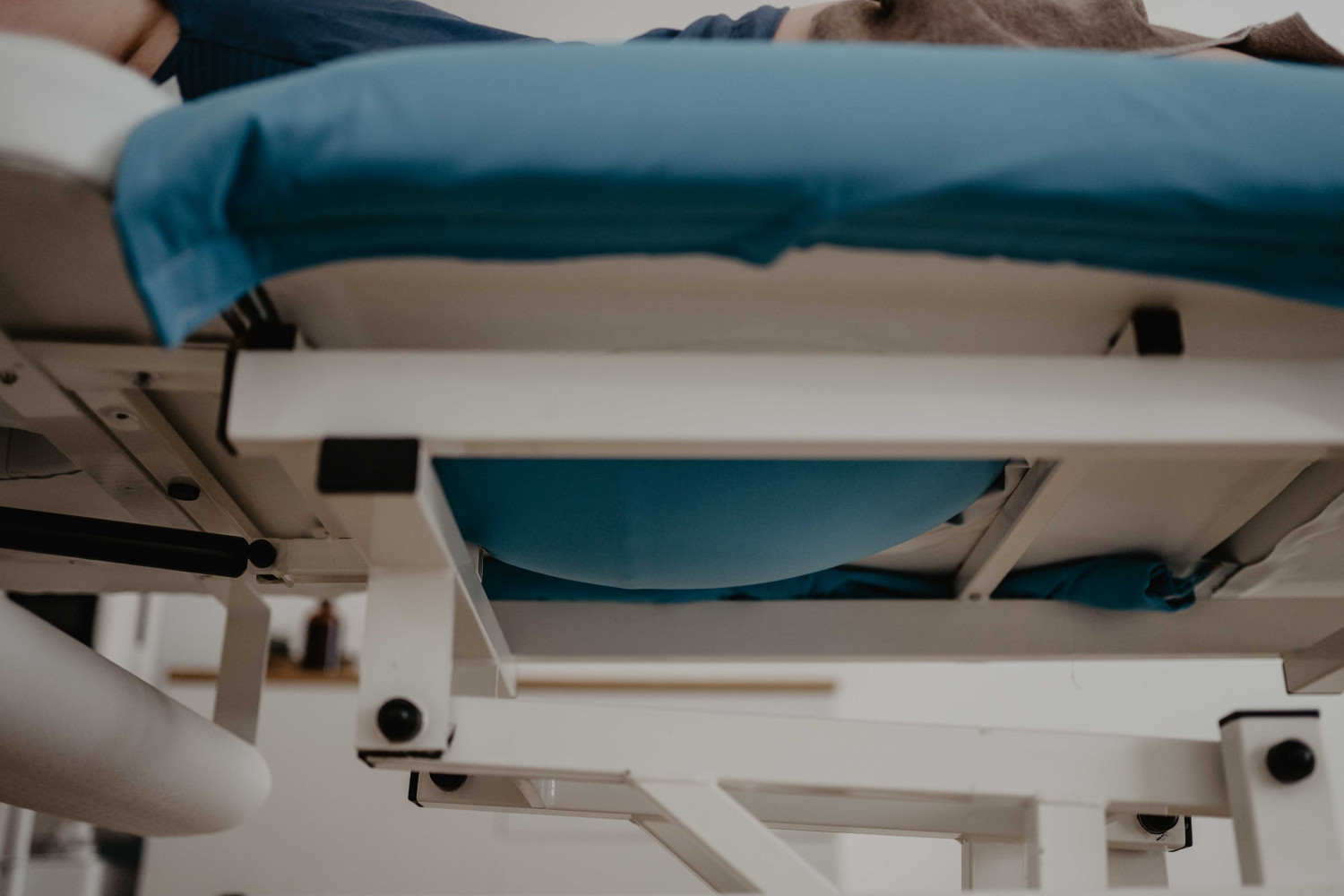
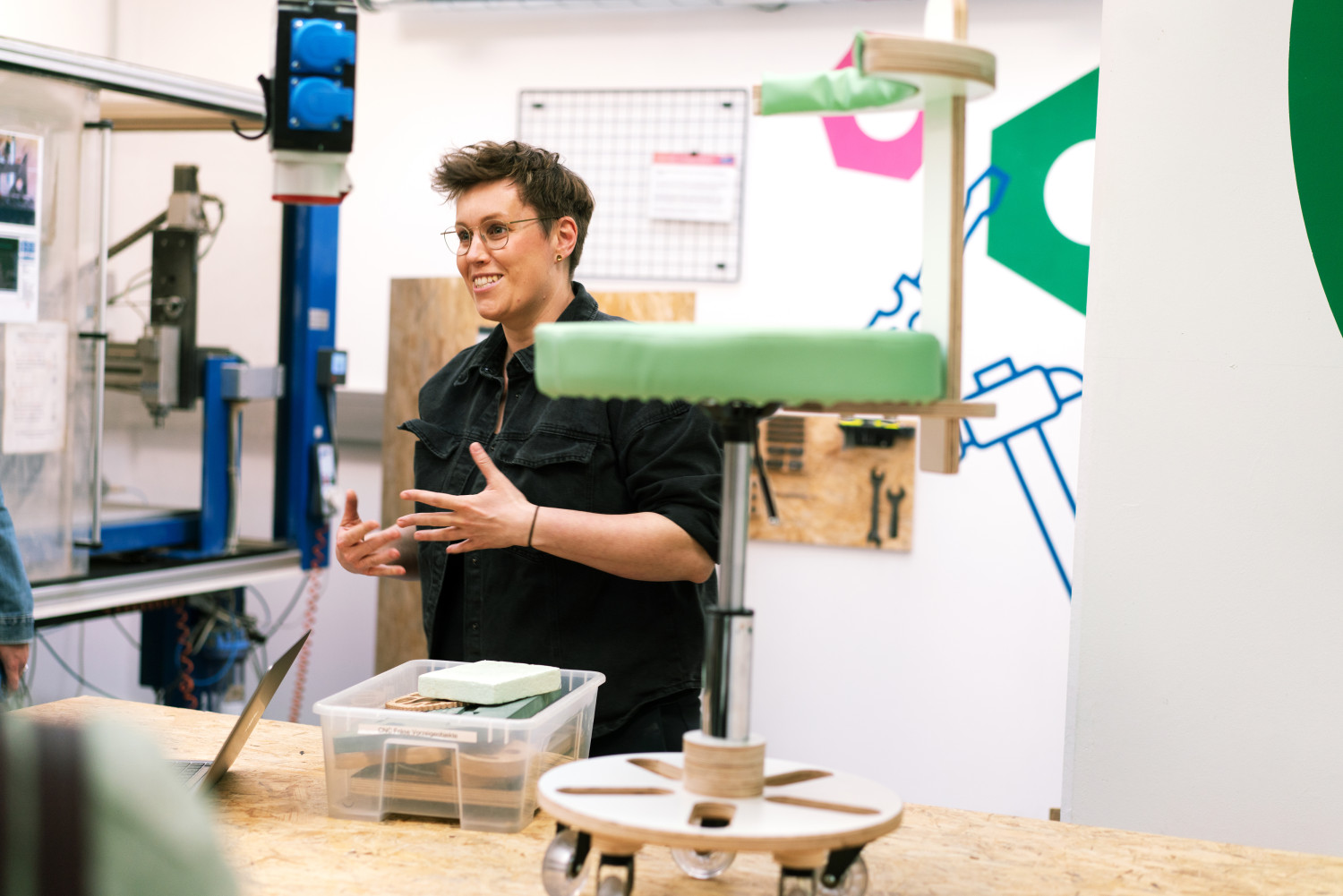