Die Idee, Workshops aus dem Happylab mobil zu machen, gibt es schon seit längerer Zeit. Nun ist es soweit: unser Mobile Maker Lab ist da! Und nein, es ist kein großer Truck, sondern eine kleine, feine und umweltfreundliche Alternative. Nämlich ein Fahrradanhänger ausgestattet mit einfachen, mobilen Produktionsmaschinen.
Der Anhänger basiert auf einem Open Source Design von "Carla Cargo" und wurde von Roland Stelzer und Gerhard Hirt aus dem Happylab-Team in den vergangenen Monaten komplett im Happylab gebaut. Dafür haben die beiden u. a. geschweißt, gesägt, lackiert und sogar ein Teil eines alten Kinderfahrrads upgecycelt.
Wir haben bei den beiden nachgefragt, was sie motiviert hat, wie die Arbeiten daran verlaufen sind und wohin die Reise mit dem flexiblen Lab jetzt hingehen soll.
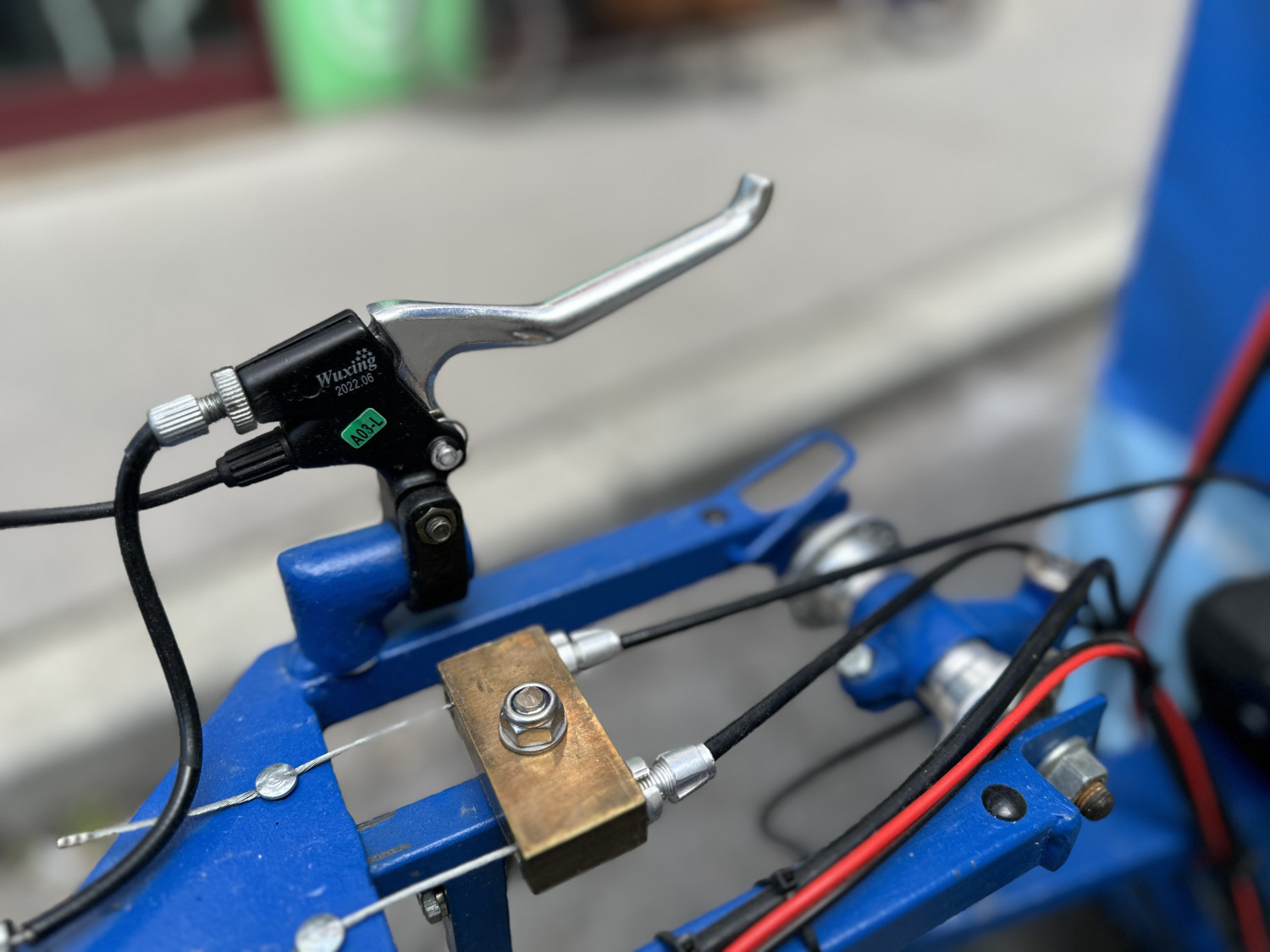
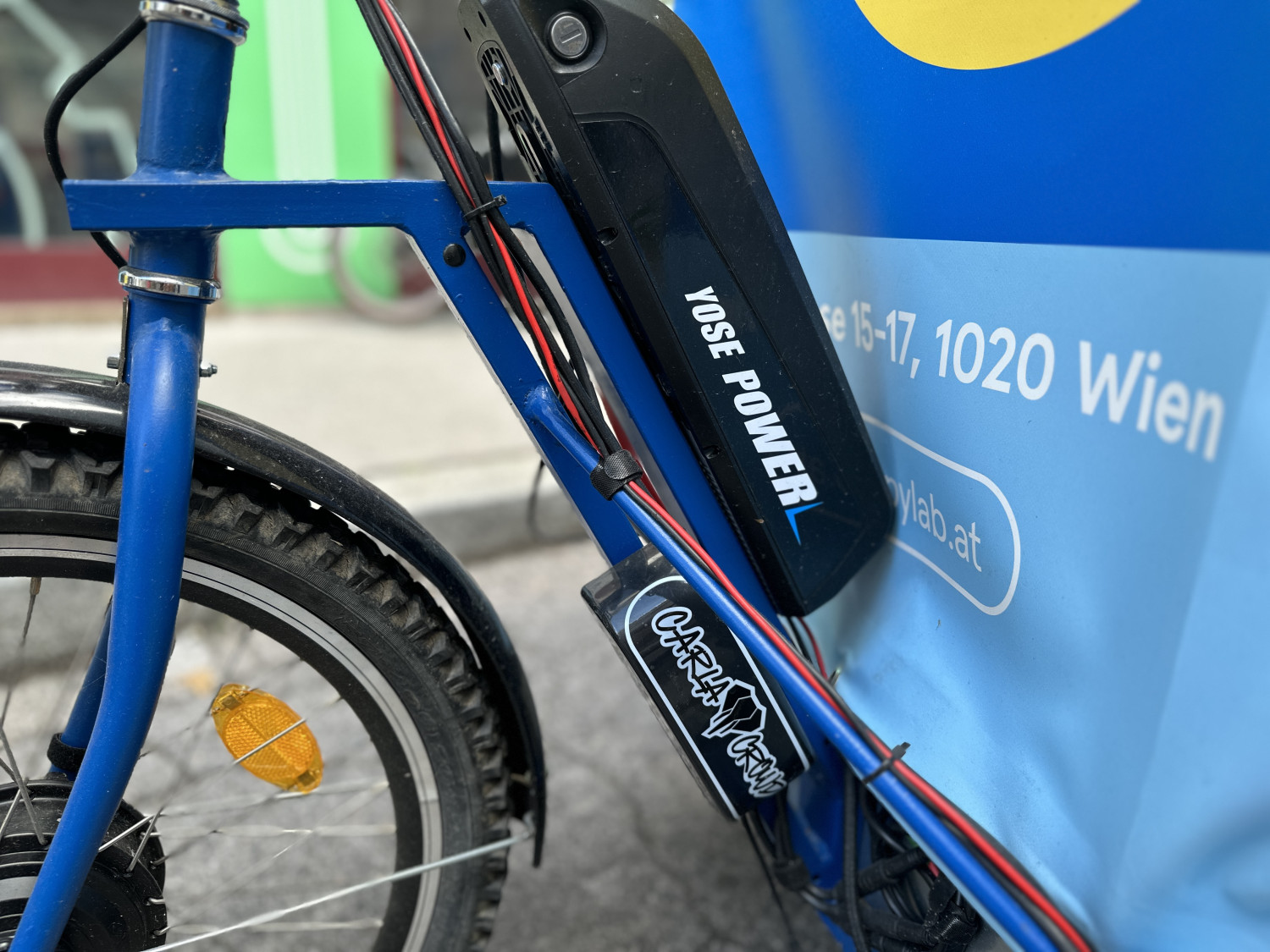
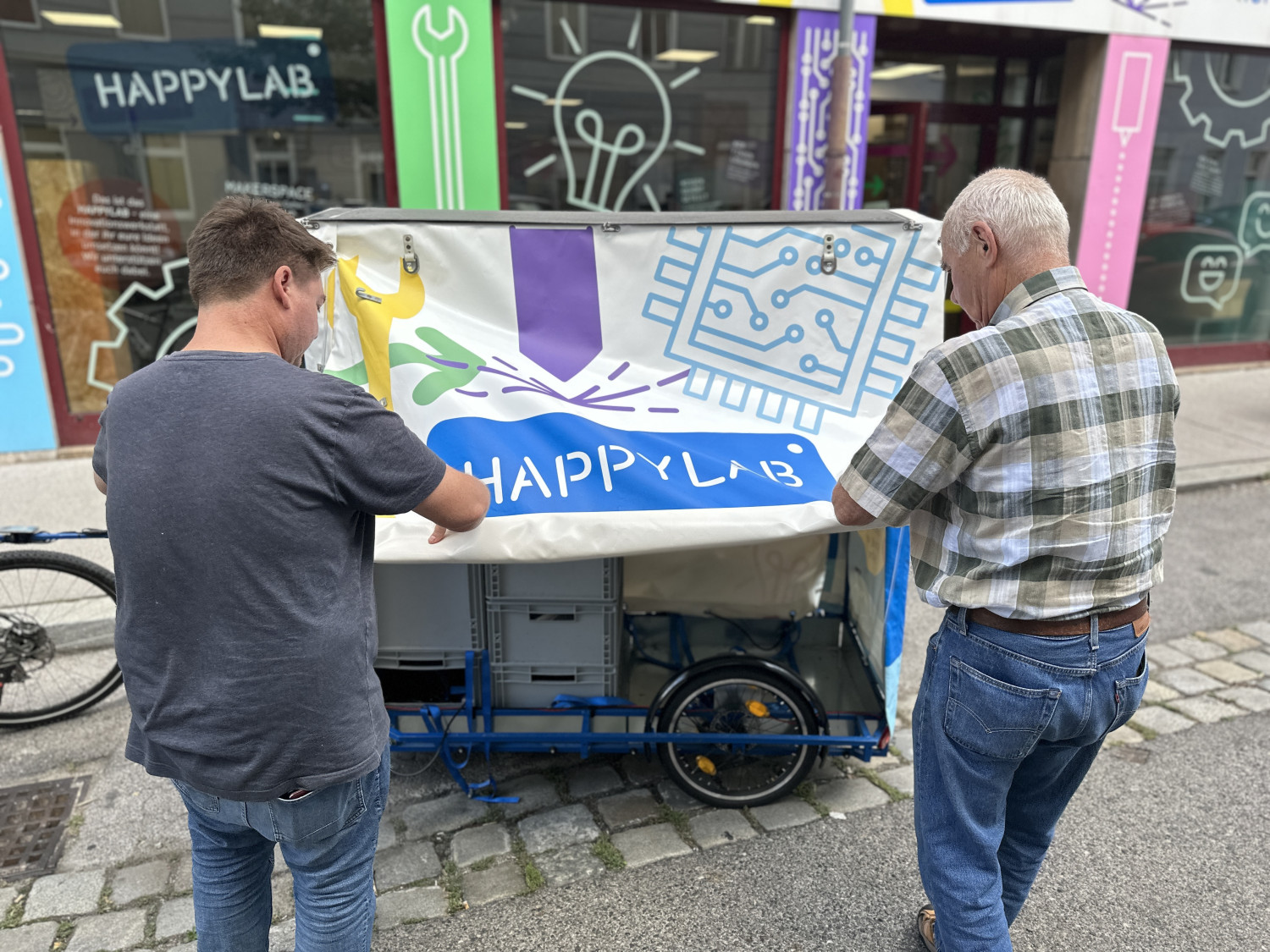
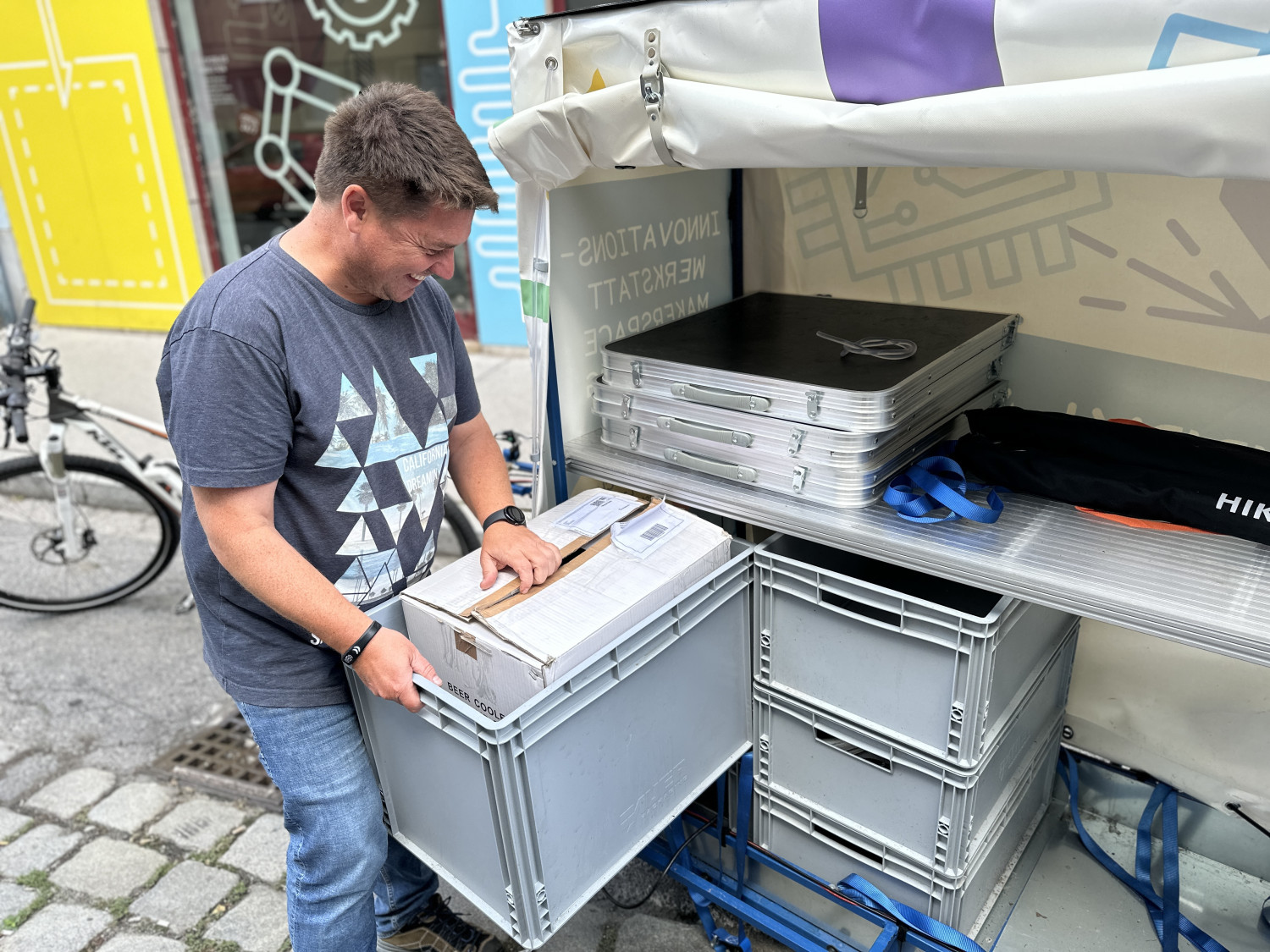
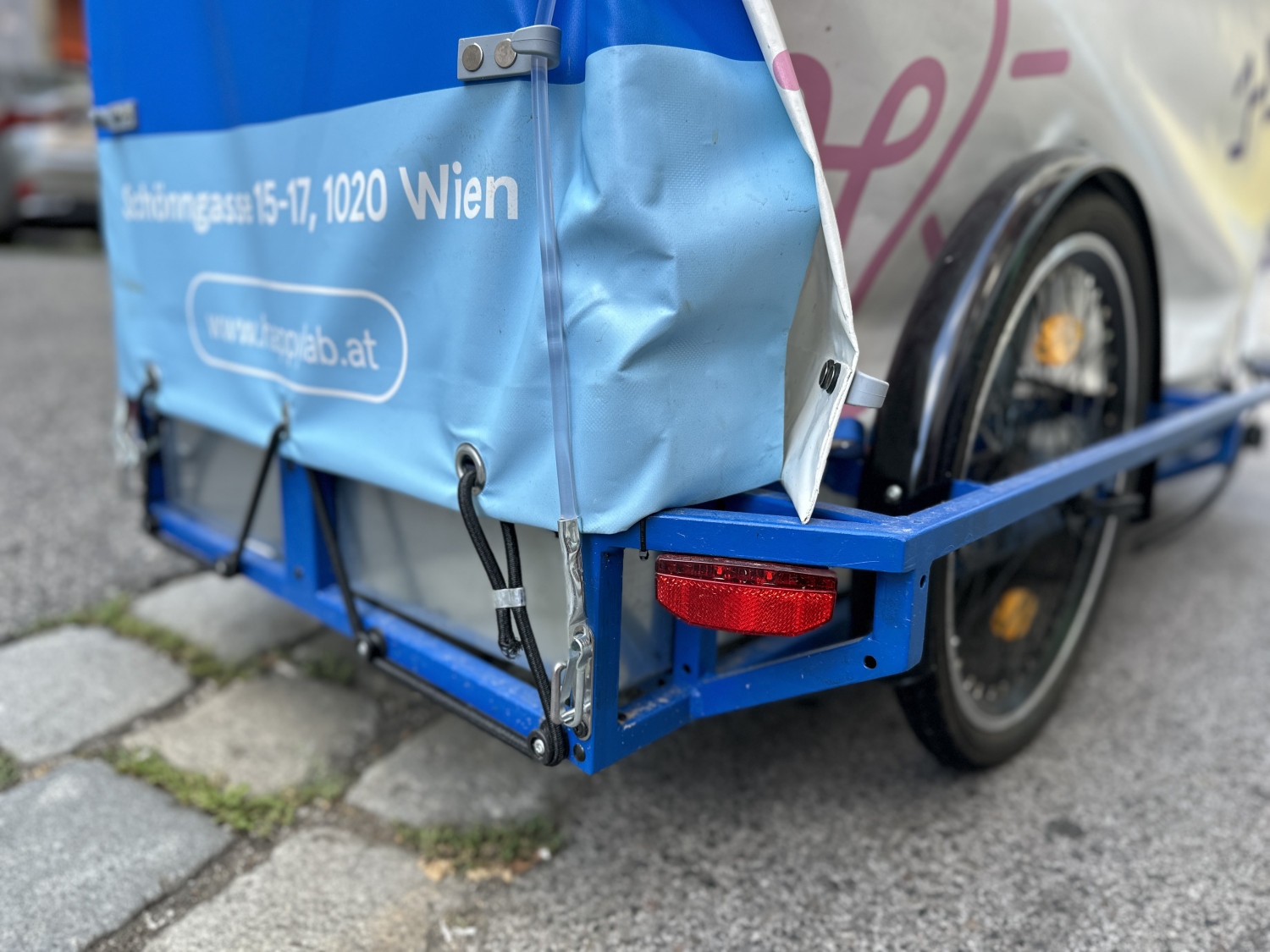
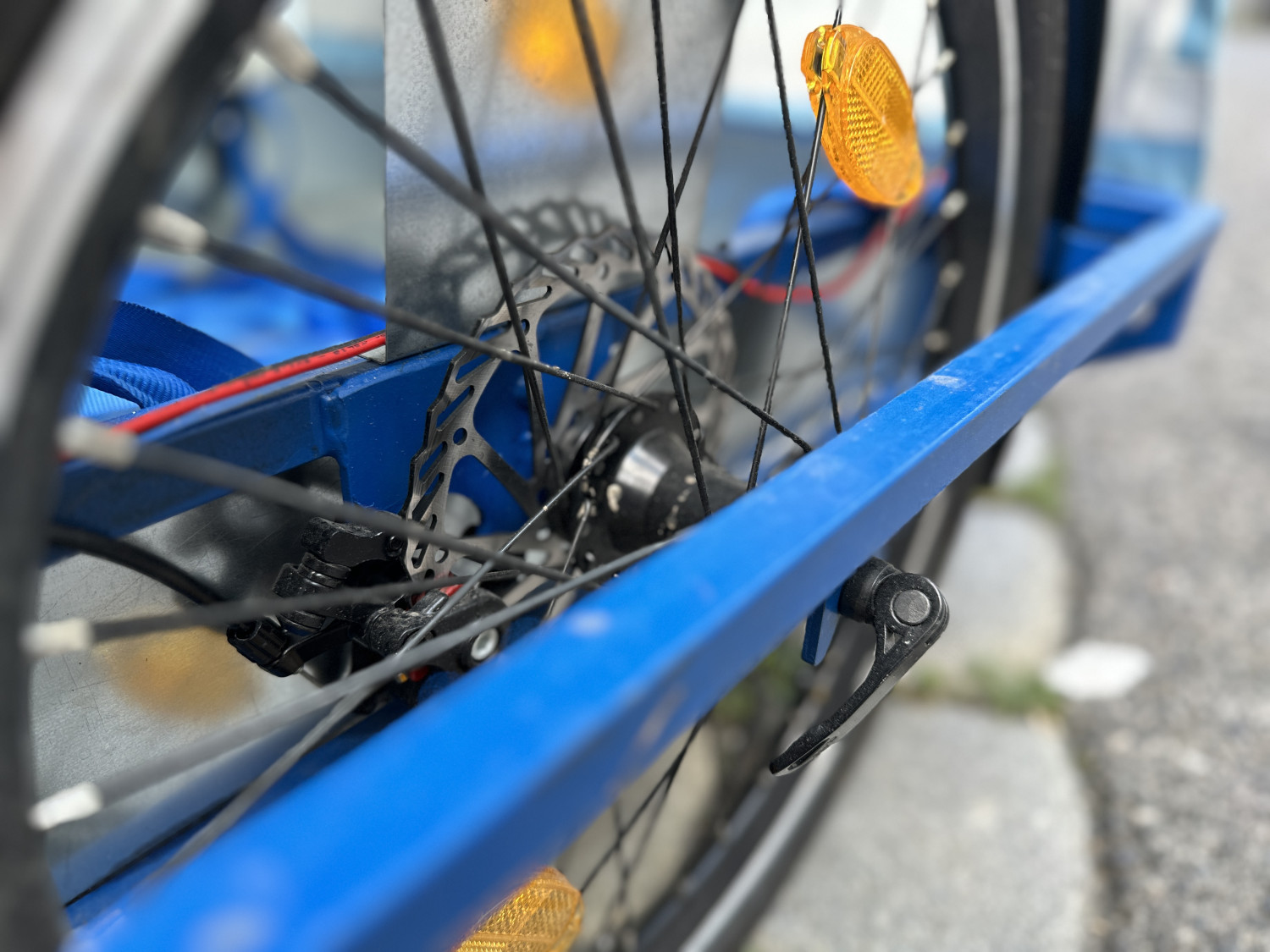
NACHGEFRAGT BEI ROLAND UND GERHARD
Wie seid ihr auf die Idee gekommen, diesen Radanhänger zu bauen?
Roland: Wir haben uns gedacht, es ist einfach cool, so ein Mobile Maker Lab mit dem Fahrrad transportieren zu können. Mit einem Auto hätten wir laufende Kosten gehabt und der Umweltaspekt war natürlich ebenso entscheidend.
Wir wollten auch einen anderen Weg gehen als viele anderen Fablabs. Unser Anhänger kann individuell bestückt werden – je nach Workshop befüllen wir die integrierten Boxen so, wie wir sie gerade brauchen. Fix oben aufgebaut ist ein kleines Solarkraftwerk, damit wir Strom zur Verfügung haben, um verschiedene Geräte zu bedienen.
Wie habt ihr den Plan erstellt?
Gerhard: Das Anhänger-Gestell selbst konnten wir wirklich als Ganzes mit den Open Source Plänen von Carla Cargo bauen. Den Rest – also Aufbau, Plane und Co – haben wir Learning by Doing entwickelt. Wir haben uns gefragt „Was wollen wir machen?“ und dann angefangen zu messen. Wir haben die Maße der Normboxen genommen und danach den Aufbau konstruiert.
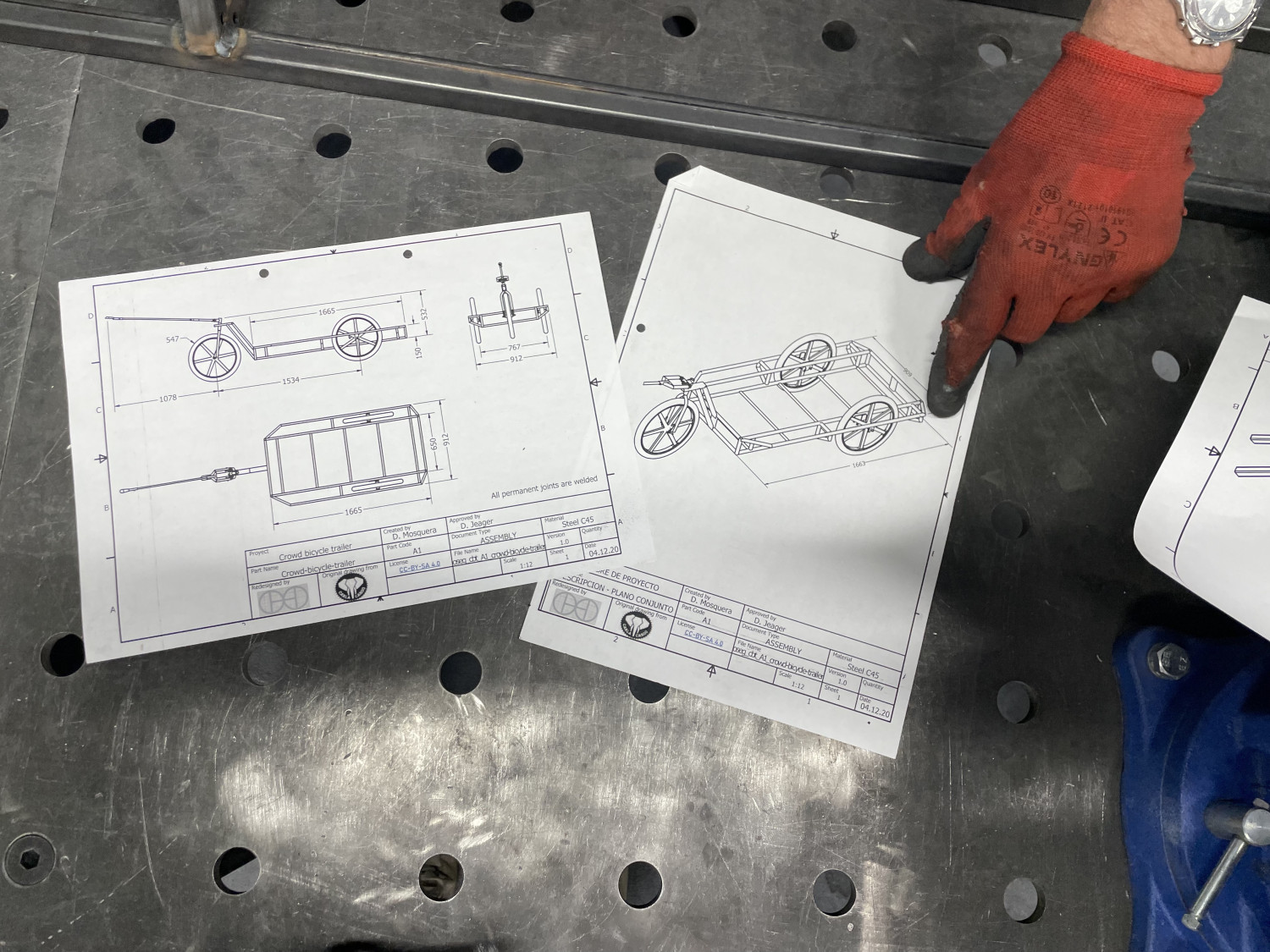
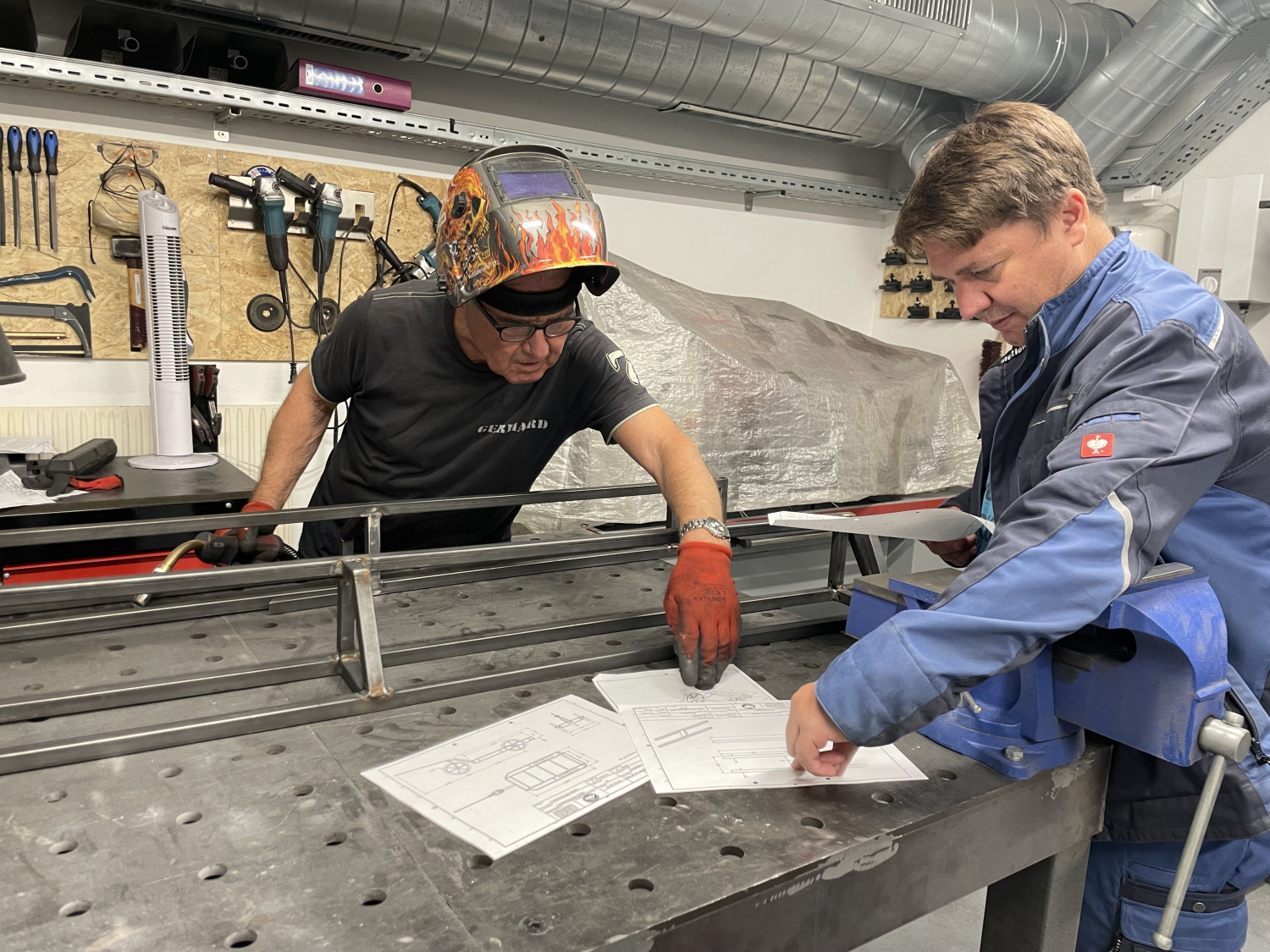
Welche Materialien und Maschinen habt ihr dazu benutzt?
Roland: Der Rahmen ist aus Stahl. Weiters haben wir Fahrradkomponenten, einen Nabenmotor plus Steuerung und eine Plane verbaut. Und wir haben auch geschaut, was wir so an Material im Lab zur Verfügung haben und dieses gebrauchte Material upgecycelt.
Gerhard: Wir haben unterschiedliche metallverarbeitende Maschinen benutzt: eine Bandsäge, um die Stahlrohre zuzuschneiden. Dann den Schweißtisch und ein Schweißgerät, in diesem Fall das MAG-Schweißgerät. Zum Verschleifen der Schweißnähte haben wir eine Flex verwendet. Und diverse Handwerkzeuge. Lackiert haben wir im Finishing-Raum und am Elektronikplatz haben wir zum Beispiel Kabel fürs Licht und die Steuerung gelötet. Die Plane und das Solarpaneel haben wir bestellt.
Gab es Herausforderungen?
Gerhard: Gar nicht so viele. Die Elektronik hat manchmal ein wenig gesponnen, aber das haben wir gut hinbekommen. Und das eine oder andere Zubehör haben wir falsch bestellt. Aber da haben wir viel gelernt.
Roland: Wobei ich mir schon ein wenig unsicher war, ob das mit den Bremsen wirklich gut funktioniert. Denn der Anhänger kann vollbeladen über 200 kg haben. Und er hat ja Auflaufbremsen, das heißt, sobald er auf das Zugfahrzeug aufläuft, bremst er. Das war spannend beim ersten Mal Bergabfahren. Aber das hat von Anfang an erstaunlich gut funktioniert.
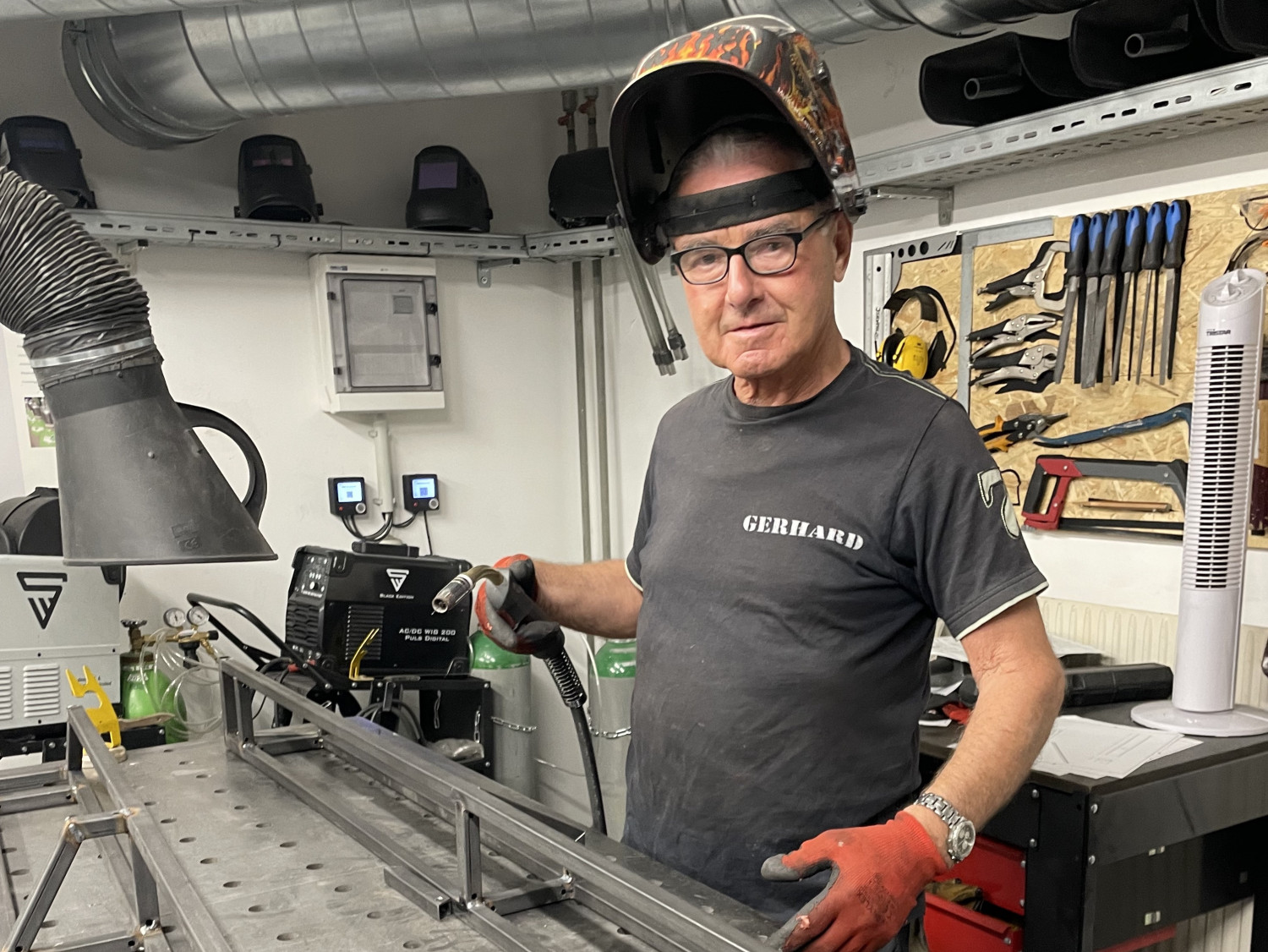
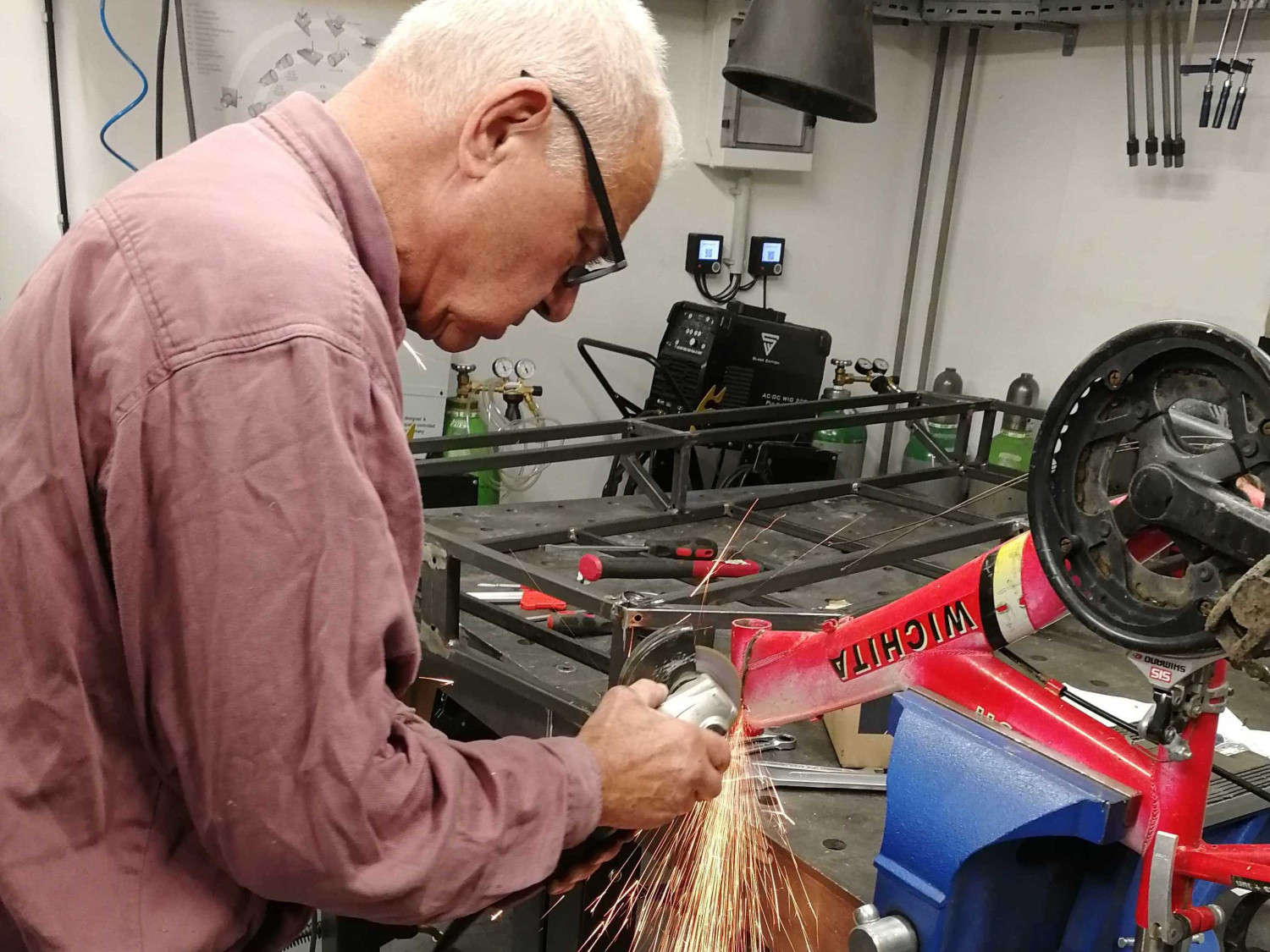
Was soll jetzt damit passieren?
Roland: Die Jungfernfahrt war ja unser Sommerfest auf der Donauinsel. Da hatten wir von Griller bis Getränkekühler alles dabei. Das war die Taufe – im wahrsten Sinne des Wortes, denn es hat geschüttet.
Und für die Zukunft haben wir verschiedene Ideen. Im Herbst veranstalten wir mit A1 Workshops für Jugendliche. Da bedrucken wir zum Beispiel T-Shirts. Wir sind außerdem in Gesprächen mit "the cool tool", um deren Workshops mobil zu machen. Zudem können wir in Schulen, Jugendzentren, Parks oder auf Veranstaltungen mit dem Mobile Maker Lab unterschiedlichste Sessions anbieten. Auch Teambuilding Events sind denkbar. Wir möchten jedenfalls so viele Menschen wie möglich mit den Themen Making und digitales Produzieren vertraut machen.
Gerhard: Übrigens – man kann den Anhänger auch ohne Fahrrad ziehen und zu Fuß unterwegs sein, denn er hat ja einen eigenen Motor.
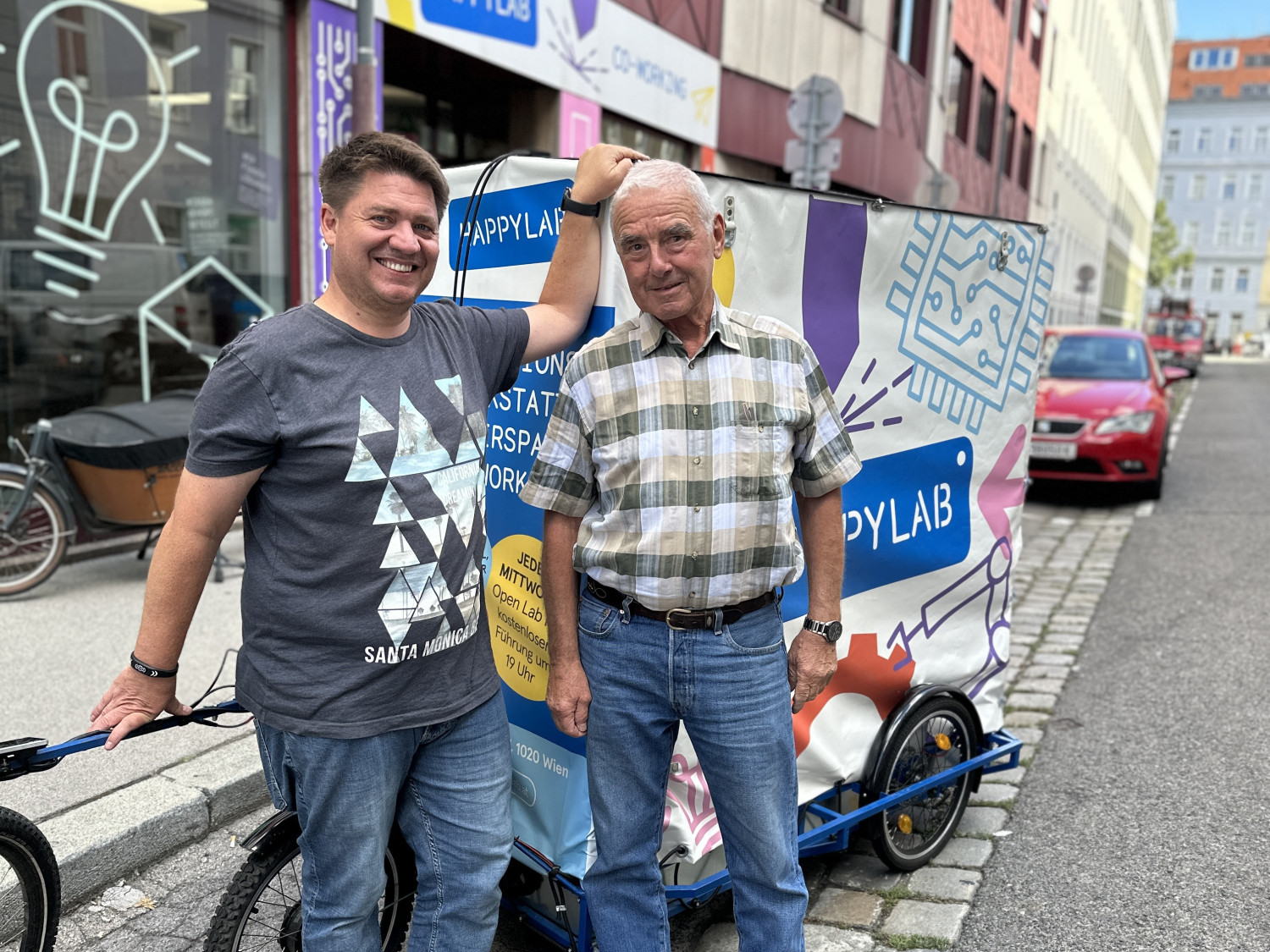